What Is the Initial Stage of the Wheel Refurbishment Machine?
The wheel refurbishment machine, initially a modified version of a standard CNC lathe, was designed to accommodate the unique requirements of automotive aluminum alloy wheels. The first-generation machines involved raising the spindle box to handle larger diameters and using standard fixtures for securing the wheels. This setup required operators to manually move the cutting tool to record coordinates and then enter them into the machine’s programming system. Though effective, this manual process was not only technically demanding but also time-consuming, with each wheel taking about 30 minutes to refurbish.
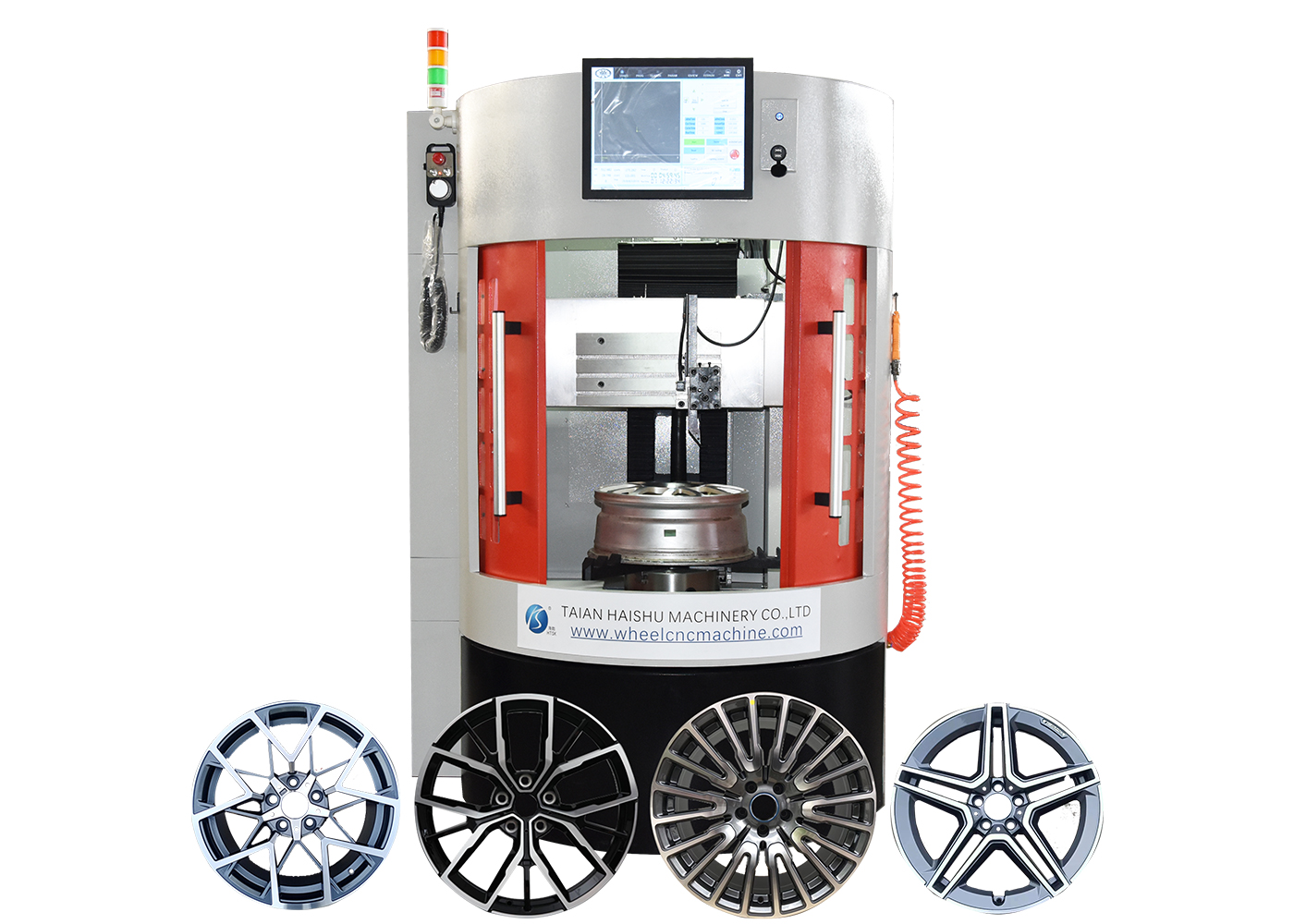
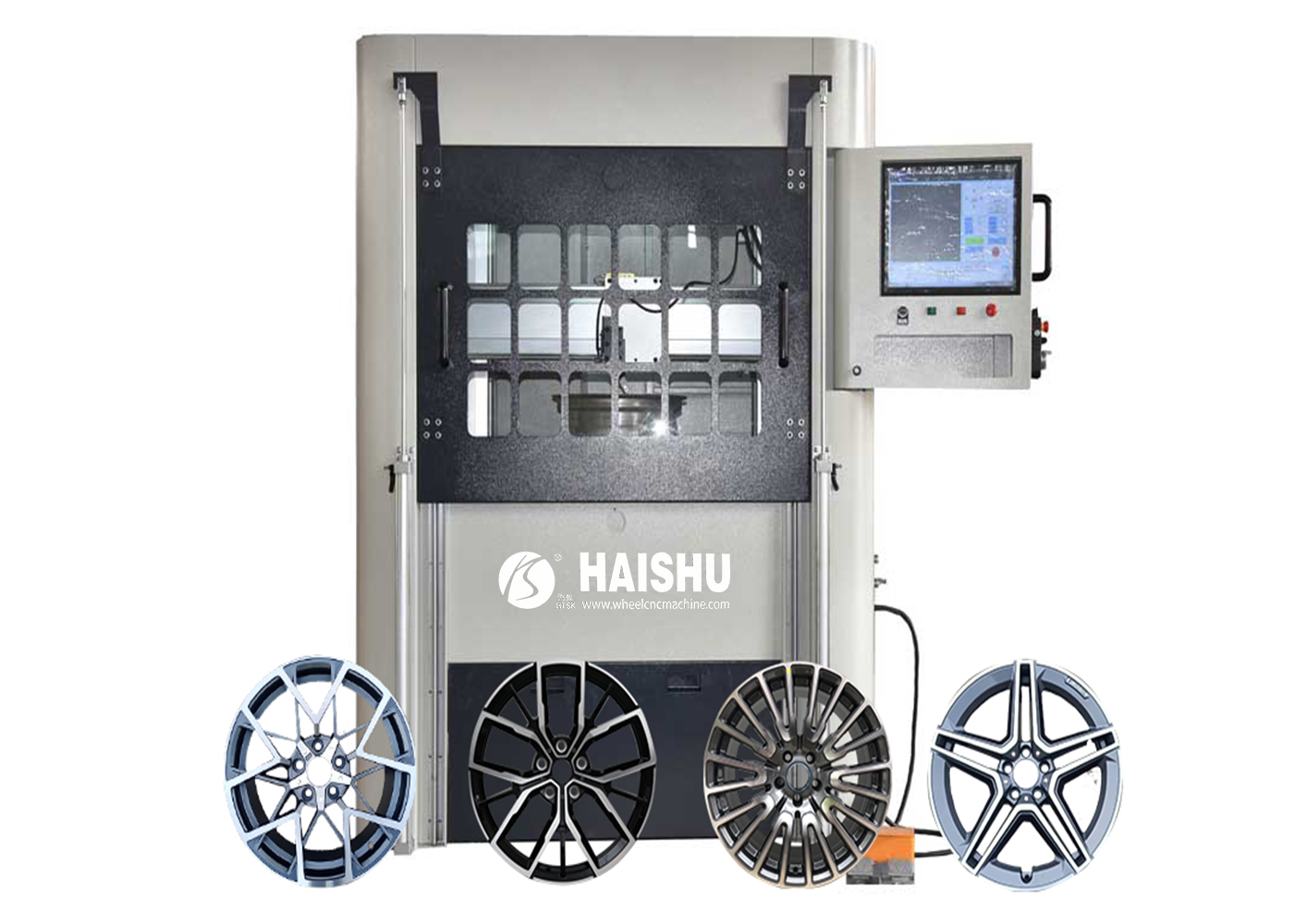
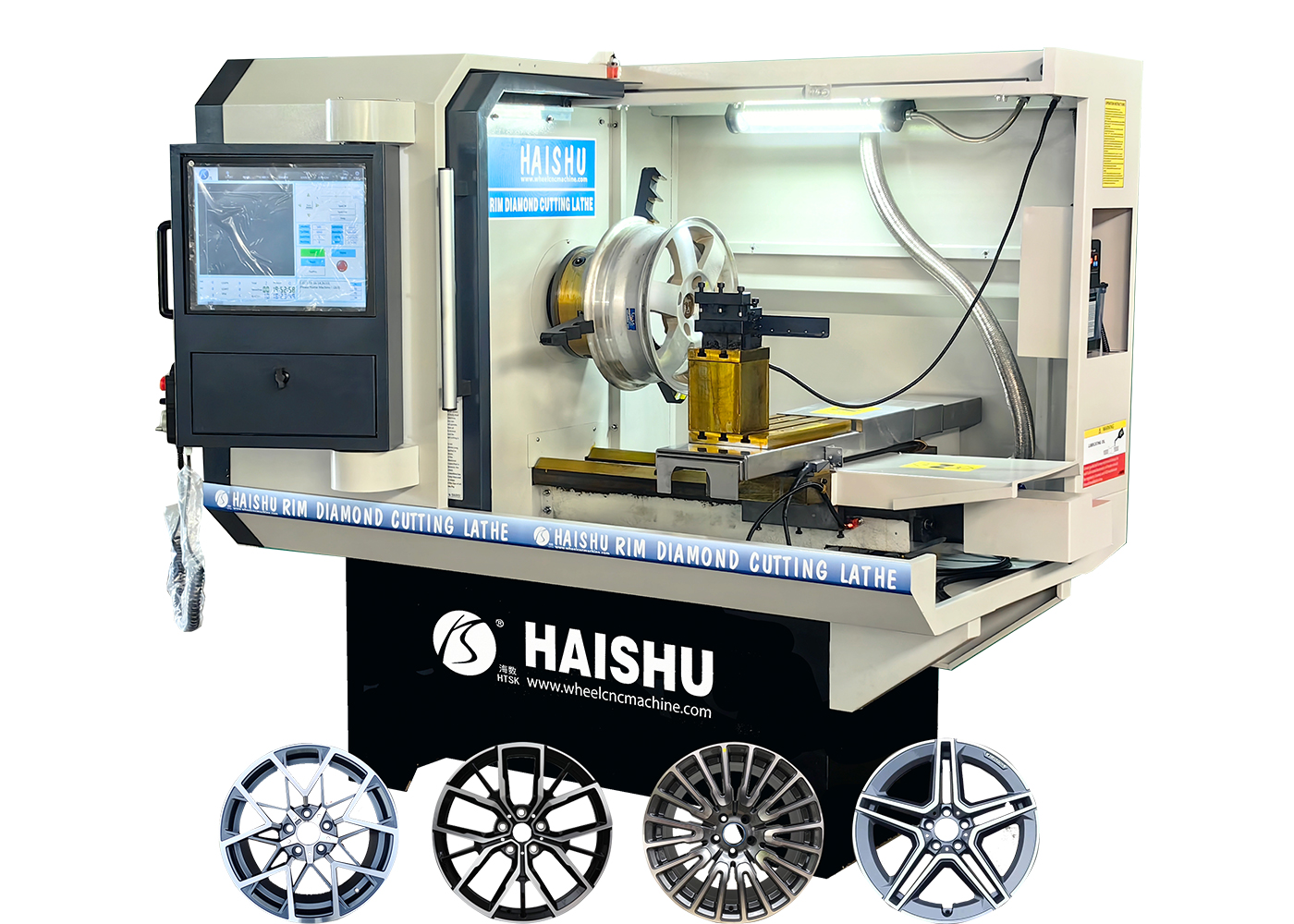
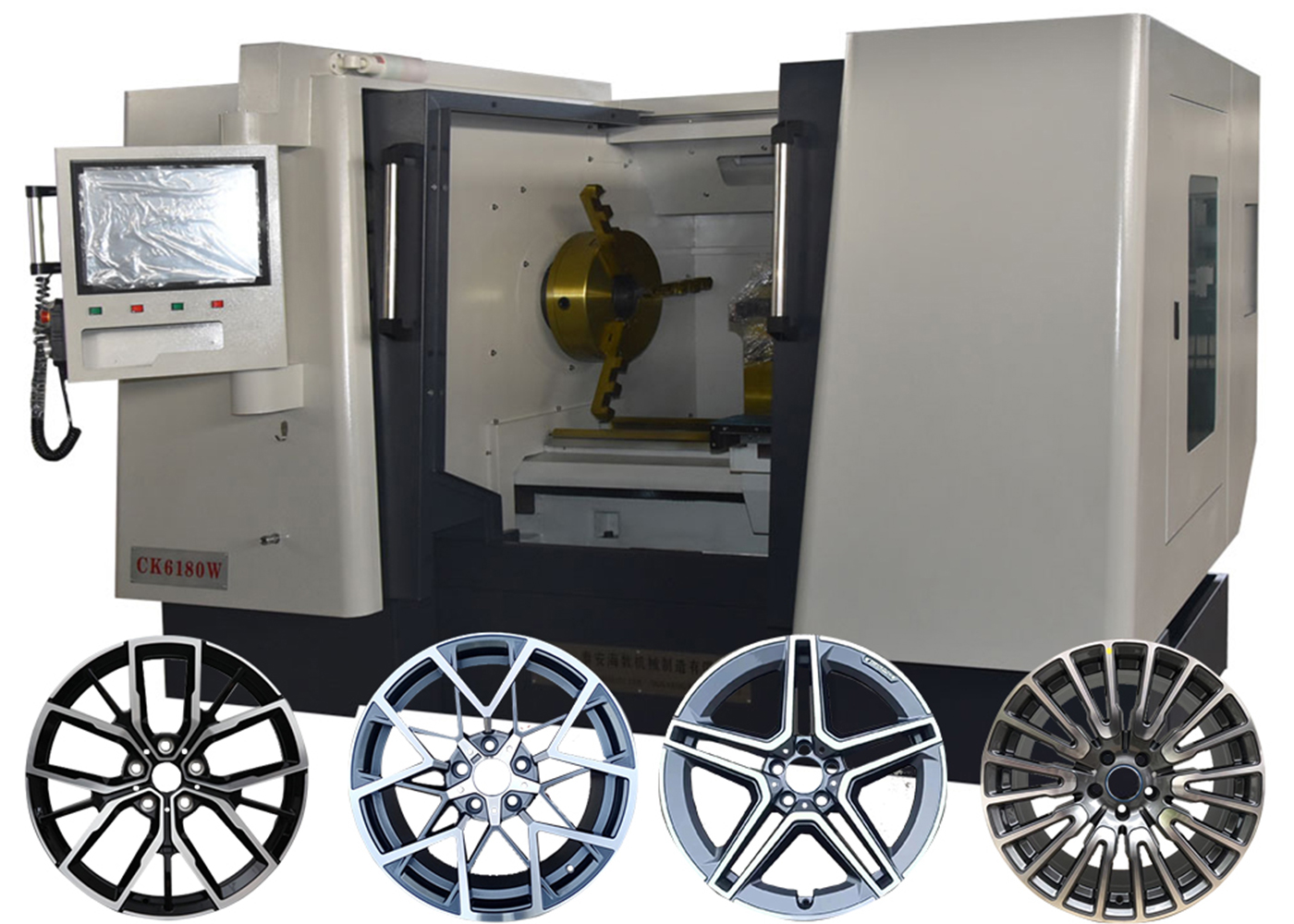
How Did the Wheel Refurbishment Machine Advance in Its Second Generation?
Building on the foundation laid by the initial models, the second-generation wheel repair lathe incorporated probe technology. This significant upgrade eliminated the need for manual coordinate recording by automatically detecting and recording precise measurements. Software improvements facilitated optimized cutting paths and automatically generated CNC programs. This enhancement saved time and reduced the technical demands on operators, although a high skill level was still necessary.
What Features Define the Third Generation of Wheel Refurbishment Machines?
Responding to market demands for greater efficiency and simpler operation, companies like HAISHU developed the third-generation wheel refurbishment machine with touchscreen capabilities. This advancement allows operators to execute tasks with the touch of a button, simplifying the entire process. These machines support multiple detection modes, including laser, probe, and cutting tools, making them versatile enough to handle various wheel types. Laser detection can be completed in as little as 20 seconds, significantly speeding up the process.
How Does the Wheel Refurbishment Machine Impact Its Industry?
The evolution of the wheel refurbishment machine from manual to fully automated systems has not only improved the quality of repairs but also provided immense convenience to industries such as automotive repair, car beauty, and 4S shops. The modern wheel reconditioning lathe, whether it’s a wheel repair lathe, wheel repair machine, wheel CNC machine, or vertical wheel repair lathe, offers high efficiency and precision, transforming how wheel repairs are conducted.
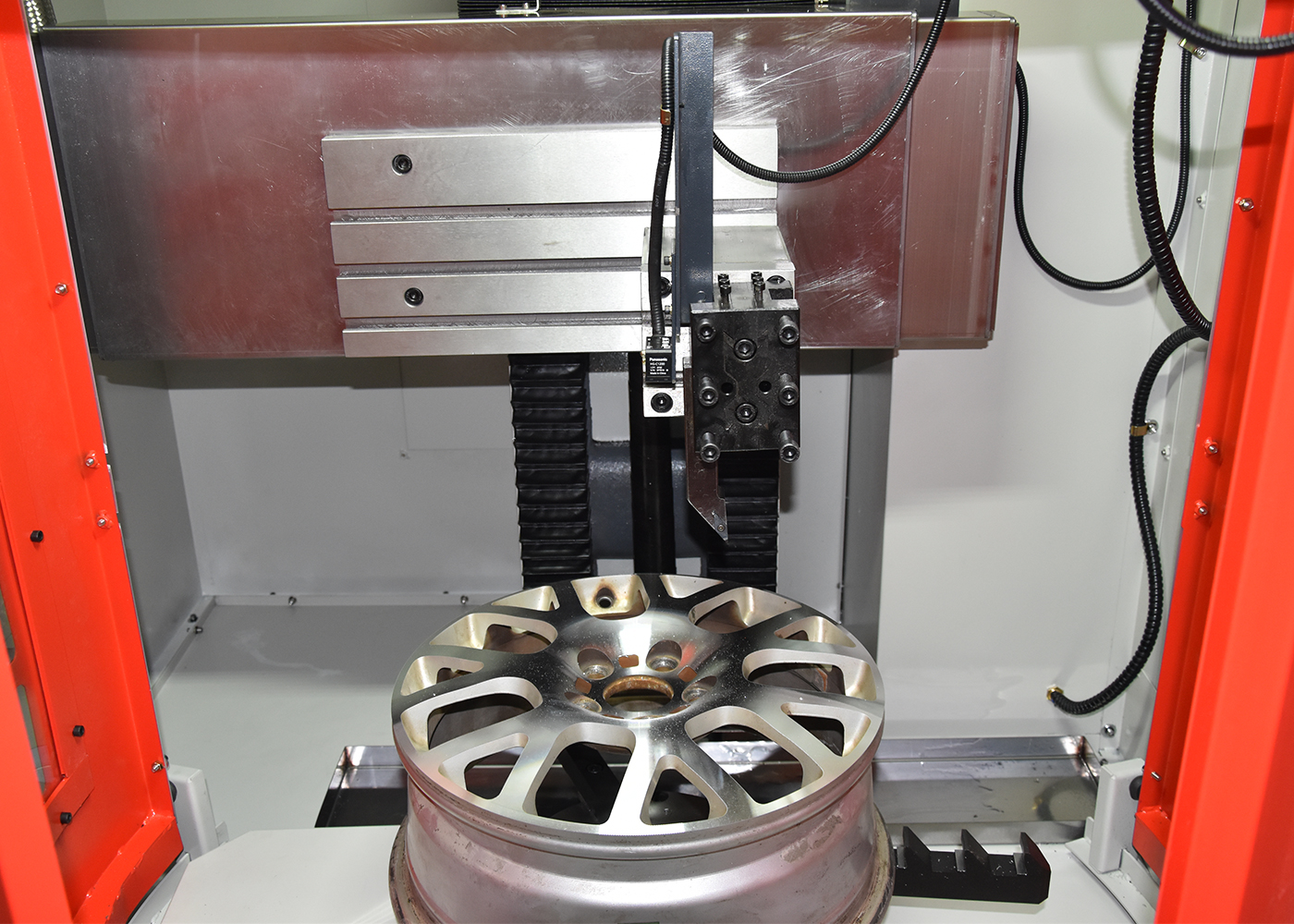
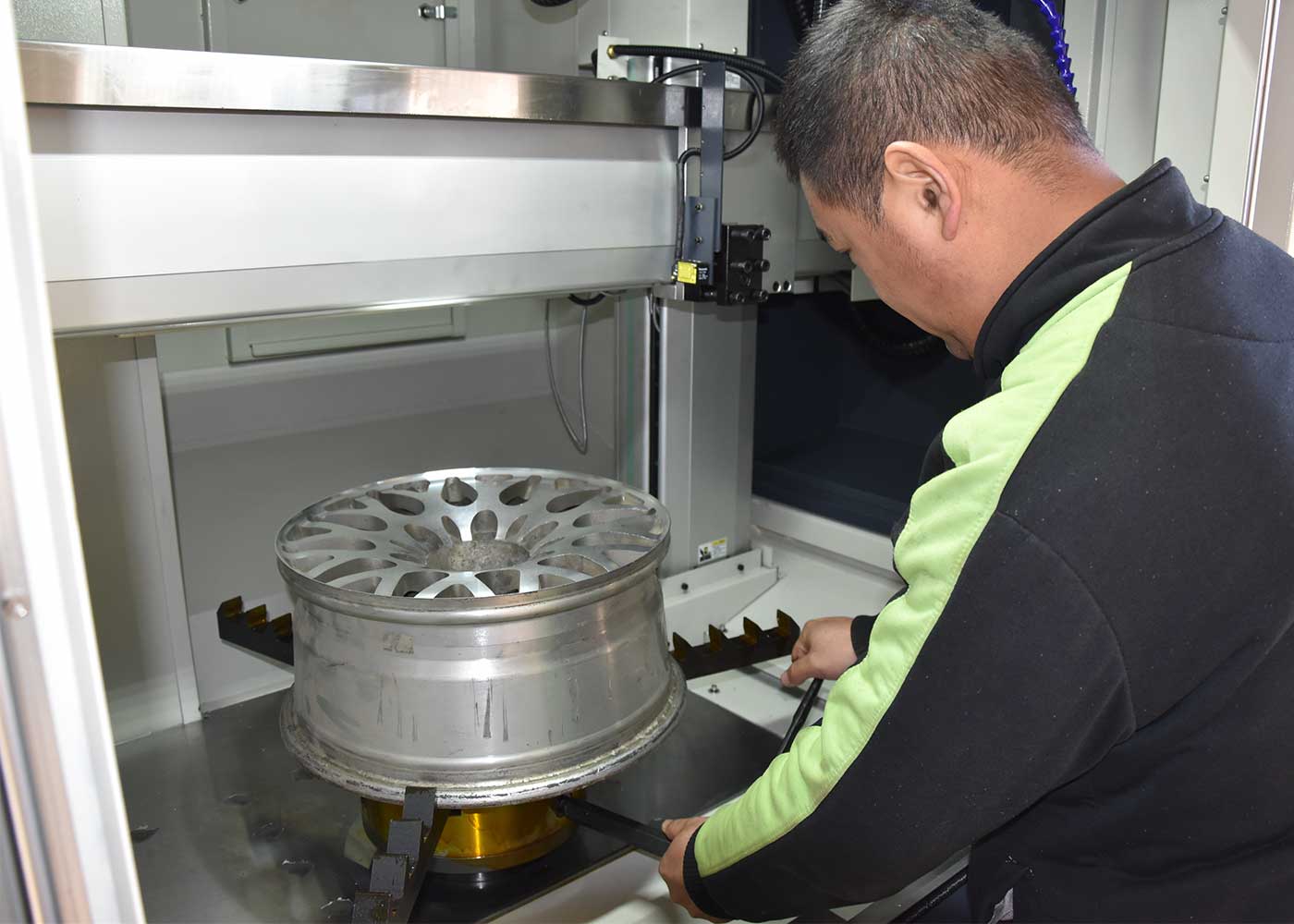
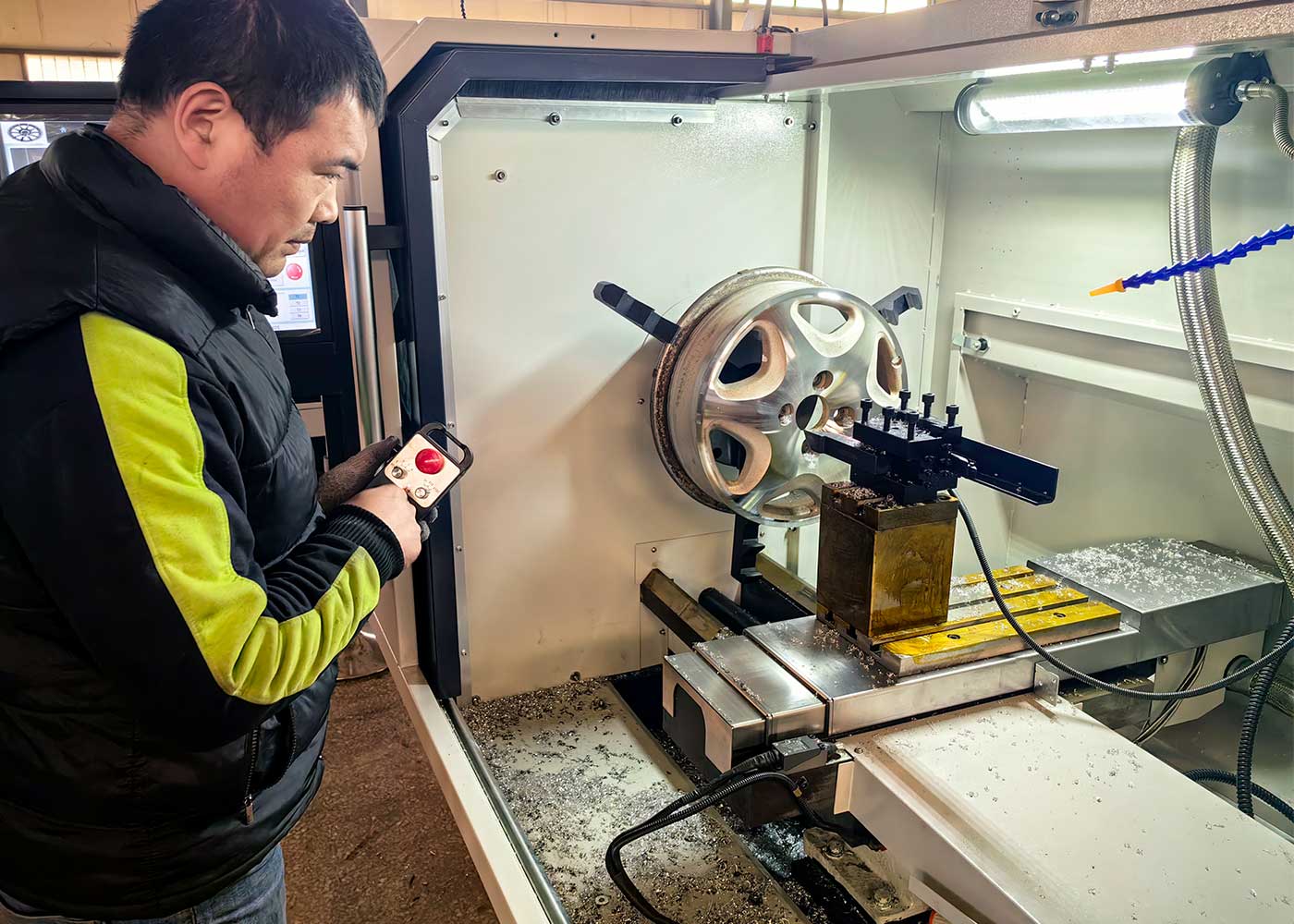
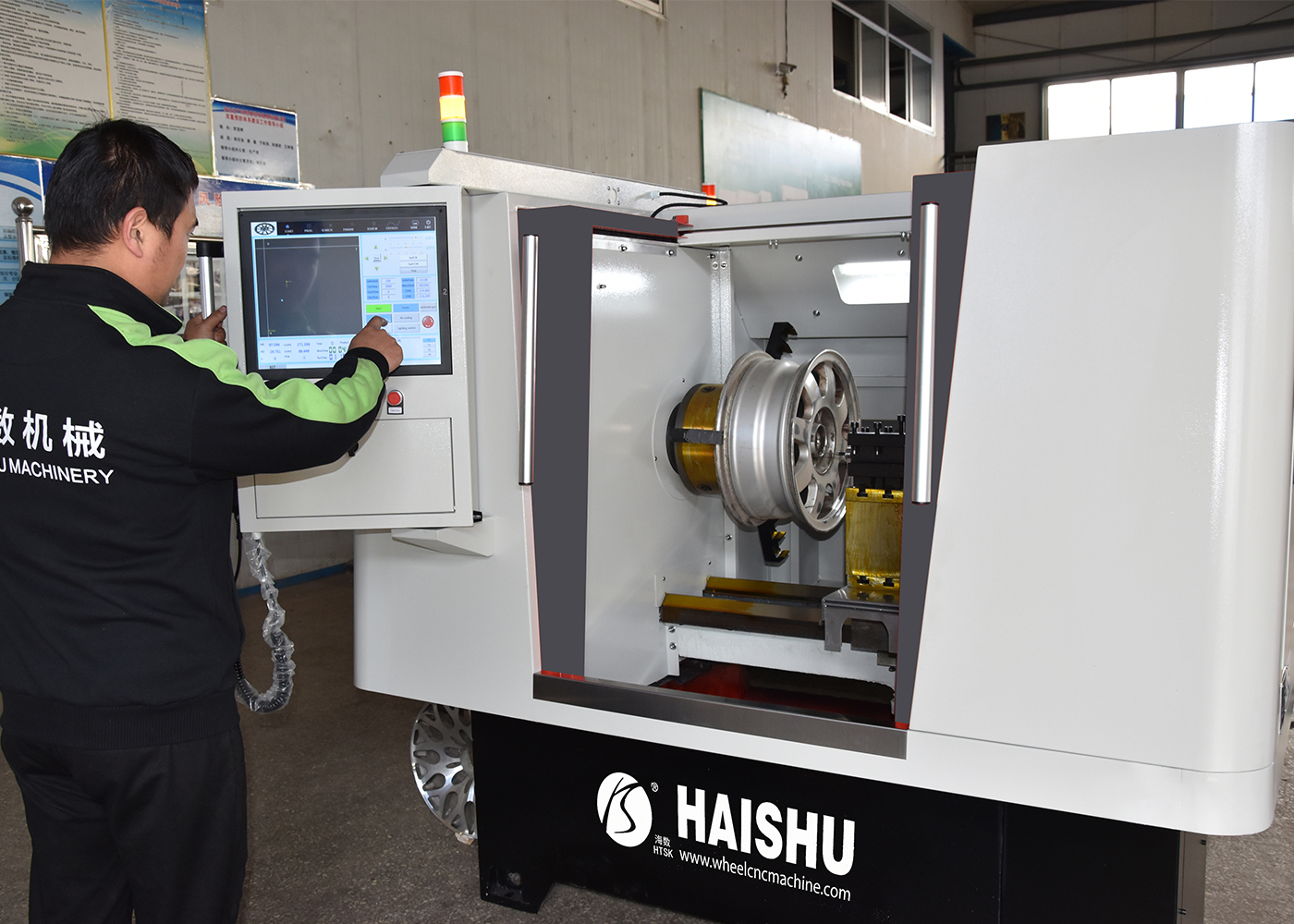
Conclusion
As technology continues to advance, the wheel refurbishment machine has shifted from manual operations to fully automated and highly efficient processes. This evolution has enhanced not only the quality of repairs but also the convenience provided to the automotive maintenance industry. For more information on HAISHU’s innovative wheel refurbishment machines, please visit our official website or contact us via email.