Alloy CNC Wheel Repair Lathe is a dedicated automotive wheel hub repair lathe. This CNC lathe enables efficient, safe, automatic, and time-saving wheel repair, meeting the customers’ precise requirements. The Alloy CNC Wheel Repair Lathe offers a range of models and types, including horizontal and vertical wheel repair lathes, linear guide wheel repair machines, CNC wheel repair machines, and more. To assist customers in selecting the most suitable Alloy CNC Wheel Repair Lathe, we will provide valuable advice from various dimensions and perspectives.
When selecting a CNC alloy wheel repair lathe, it’s crucial to consider the purpose and scope of your business. This involves determining the specific requirements for repairing alloy wheels, such as the size range of the wheels you’ll handle. The mainstream automotive wheel hub sizes typically range from 12 to 23 inches, although larger sizes like 32 inches exist for certain types of vehicles, such as pickup trucks. Considering the size range within your business scope is essential.
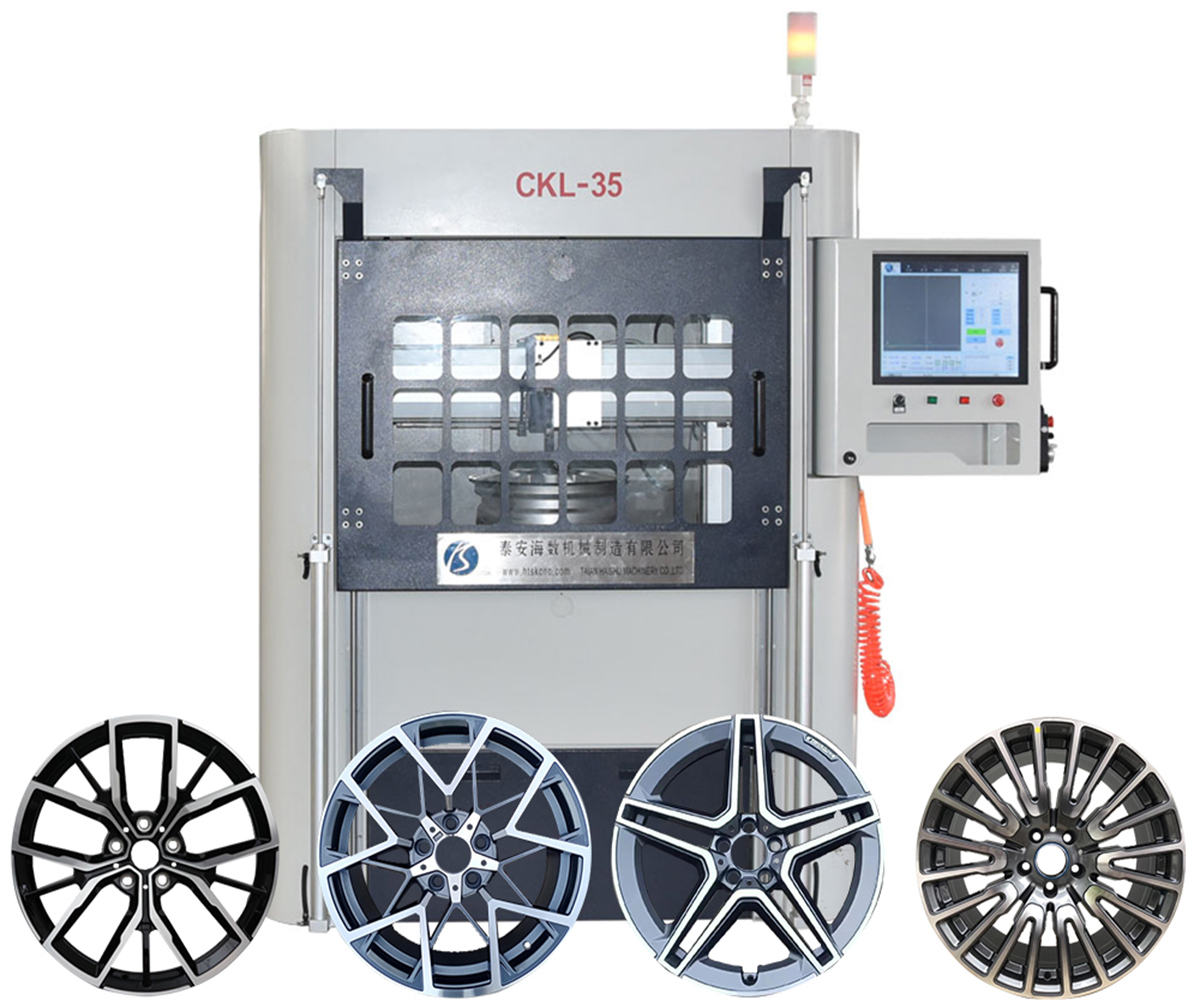
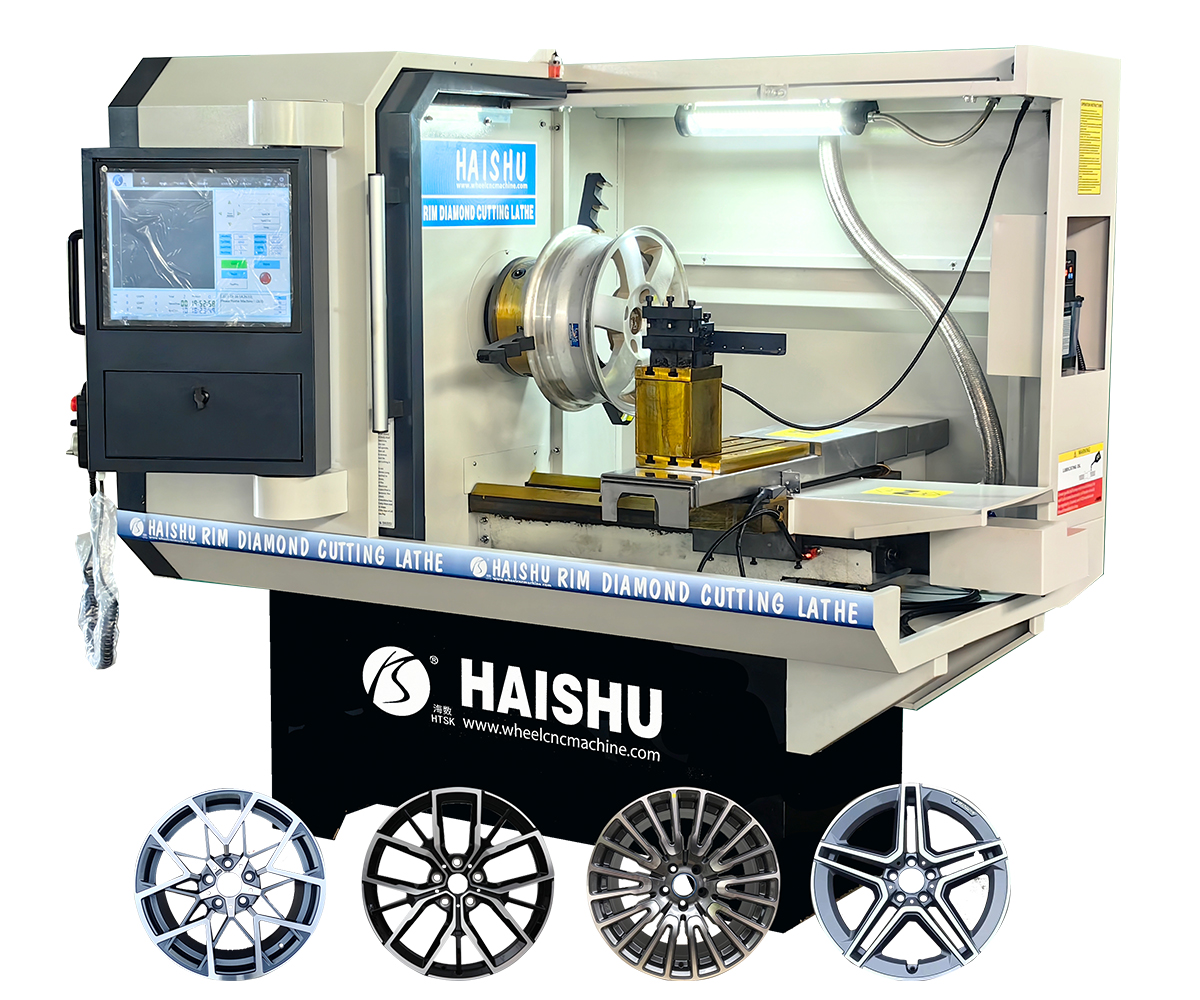
Additionally, there are different types of CNC alloy wheel repair lathes available, including those with hardened or linear guideways, as well as universal or specialized systems. Probe detection methods, such as laser detection or probe detection, can also vary. It’s worth noting that for aluminum alloy wheel hubs, linear guideways are often preferred due to their ability to achieve a brighter and cleaner surface finish. Specialized wheel repair software, tailored to the shape of the wheel hub, can optimize the repair process and generate programs automatically, offering a user-friendly and efficient operation.
When it comes to the structural design of the lathe, horizontal configurations are suitable for smaller wheel hubs, while vertical wheel repair lathes excel in processing larger wheel hubs or operating at high speeds. However, vertical lathes typically have a higher price point, so budget considerations should be taken into account when making a selection.
By considering these factors comprehensively, you can make an informed choice when selecting a CNC alloy wheel repair lathe that meets your specific requirements and contributes to the success of your business.
The second consideration is the size and capacity of the CNC alloy wheel repair lathe. Find a CNC lathe that can accommodate the largest wheels you plan to repair in terms of fixture size and rotational capacity. The CNC lathe has an appropriate spindle bore size to fit wheel bearings. If your automotive wheel hub range is between 12-23 inches, when choosing a fixture for the wheel hubs, the minimum required diameter of the fixture should be around 600mm while meeting the clamping requirements. The fixture can have either three or four jaws. Within this size range, the recommended spindle model is A2-5. The chuck should also have a minimum diameter of 250mm. For larger wheel hubs, such as 32 inches, the spindle may need to be upgraded to A2-6, or if not upgraded, it should still be larger. The chuck should be even larger, possibly around 320mm. If you choose not to replace the chuck, make sure the fixture size is as large as possible to meet the requirements of customers with larger wheel hubs.
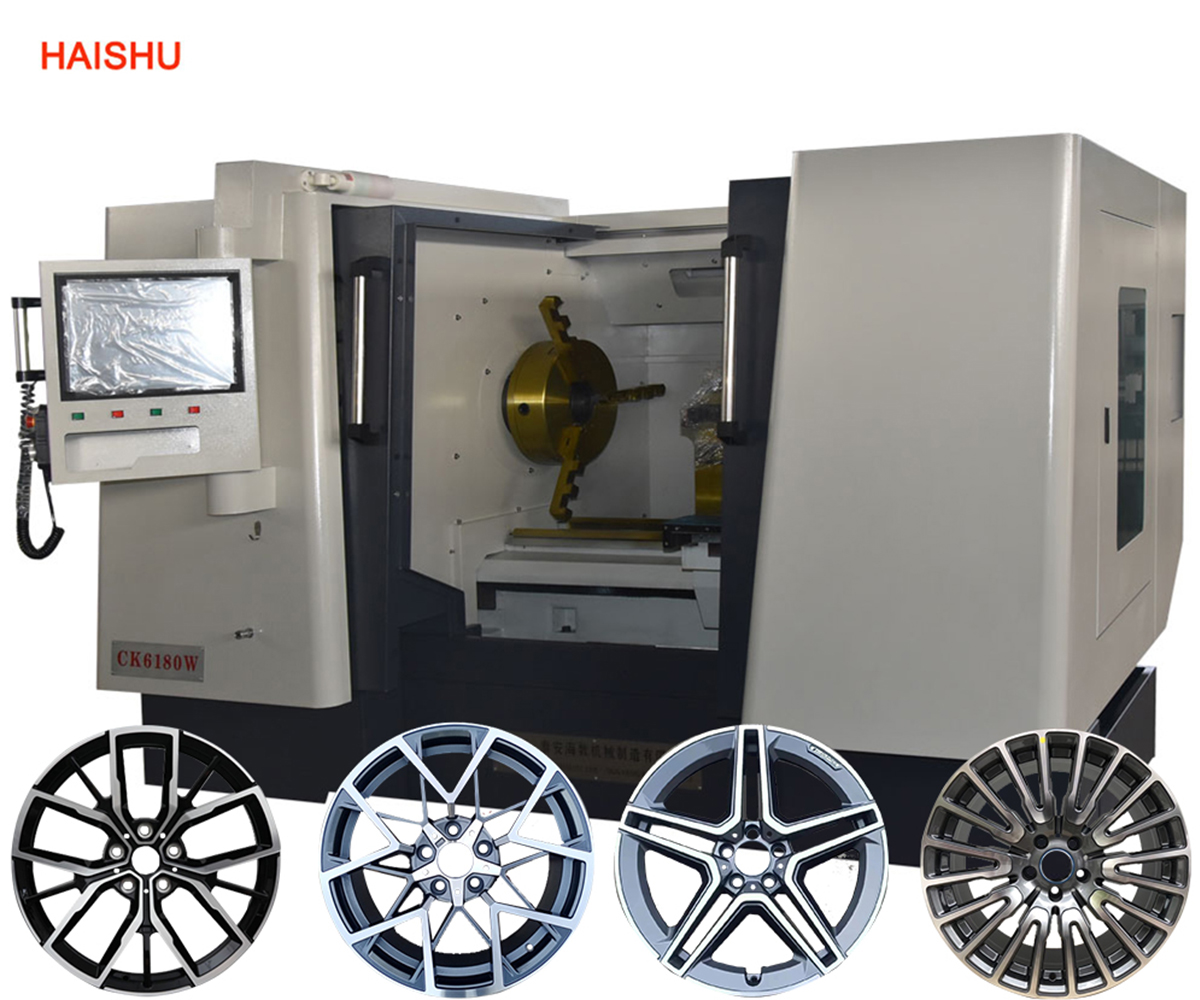
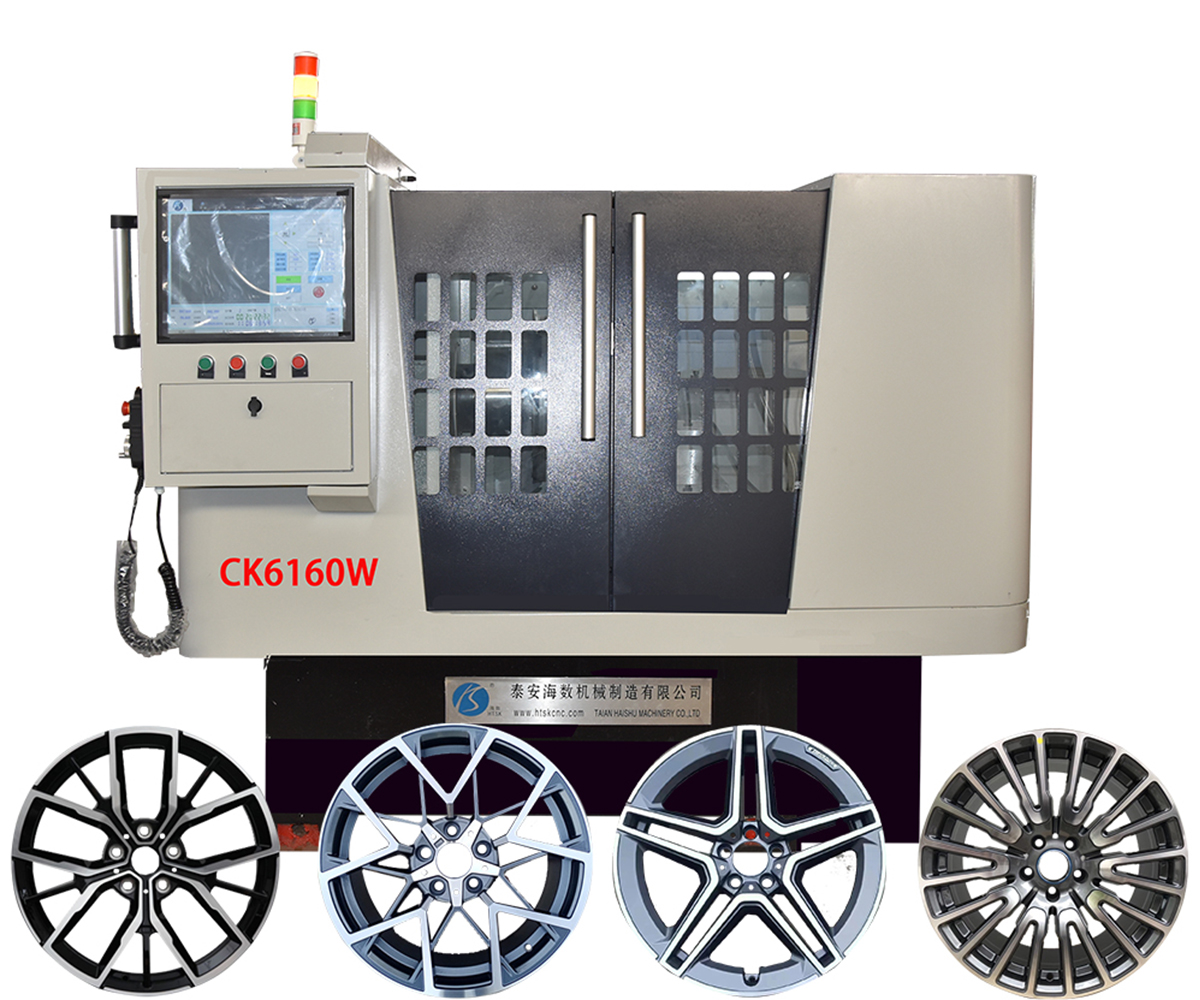
The third consideration is the structural quality of the CNC alloy wheel lathe. The construction quality and durability of the wheel repair lathe should be carefully inspected. The lathe should be robust enough to withstand the demands of wheel repair operations. The wheel repair lathe made from high-quality materials can resist excessive wear during continuous applicaton. It is important to consider the material used in the CNC wheel repair lathe. Some wheel repair lathes are welded with steel plates, some are cast iron, and others have alloy frameworks. There are various forms and structures available, each with different requirements for rigidity. If the lathe is cast iron, it generally provides sufficient rigidity. A single-column structure can be used, and the cast iron base adds weight, enhancing overall rigidity. If it is a steel plate welded structure, it is recommended to opt for a vertical structure as the CNC wheel repair lathe itself is lighter in weight, and a horizontal structure is more likely to experience vibrations. Another option is an alloy assembly structure, which offers an attractive appearance but comes with higher costs, increasing the purchasing cost for users. Moreover, an alloy structure should adopt a double-column structure to ensure both rigidity and the ability to meet the processing requirements of large wheel hubs, which is crucial.
Another important consideration is the CNC control system of the CNC alloy wheel lathe. The CNC control system is a crucial component of the wheel repair machine. The system of this wheel repair lathe should be user-friendly, intuitive, and offer a range of customizable options. Take into account the software functionality, programming interface, and ease of operation. A reliable and efficient control system can suit your specific needs. Currently, the market offers two types of CNC systems. The first type is a general-purpose system, similar to the one used in CNC lathes. This system has limited functionality and requires complex operations. It lacks laser detection capabilities and may require the assistance of third-party optimization systems for system optimization. Moreover, it is generally expensive. The second type is a specialized CNC system designed for wheel repair lathes. This CNC system not only enables laser detection but also provides probe detection capabilities. It allows for one-click automatic optimization, one-click tool setting, and customization in over 70 languages. The system’s strength lies in its ability to be customized according to specific requirements. For example, it includes a laser power control switch that can be turned off when not in use to prevent eye injuries caused by laser radiation. Additionally, it features a user-friendly touch screen interface with various graphical buttons that provide clear visibility of operations and steps. Importantly, this specialized wheel repair system is easy to learn, with mastery achievable within 30 minutes, and it is less likely to be forgotten.
Another important point to consider is the cutting tools and accessories of the wheel repair lathe. Check if the lathe is equipped with a variety of cutting tools and accessories specifically designed for repairing alloy wheels. These may include diamond cutting tools, rim repair attachments, and various wheel clamping fixtures. Ensure that the lathe supports the necessary tools and accessories required for your repair operations. When inquiring about the CNC alloy wheel lathe, make sure to ask the manufacturer about the type of cutting tools they provide to customers before shipping. The selection of the tool tip position is crucial for different wheel shapes, offering three possible directions: left offset, right offset, and center. Additionally, inquire about the available accessories for the CNC alloy wheel lathe. Basic accessories typically provided by manufacturers include damping pads and wrenches. It is crucial to clarify these details to avoid receiving the CNC wheel lathe without the necessary accessories, which could hinder its usability.
The utmost importance in a CNC alloy wheel lathe lies in precision and accuracy. Achieving optimal results in alloy wheel repair requires precision and accuracy. Seek a wheel repair lathe with high spindle speeds, smooth operation, and excellent concentricity. The wheel refurbishment lathe should possess features like automatic measurement and compensation to ensure accurate repairs. Considering these factors, I highly recommend customers to consider a linear guide rail system. It meets the requirements for both transmission efficiency and rigidity, employing real-time software that provides instant visibility of the effects of data compensation modifications. For instance, if there is a shift in the X direction, the corrective effect will be immediately apparent after modification, reducing the number of repair and machining iterations. This enables customers to achieve desired results after just one or two machining operations. Furthermore, it is important to consider surface detection for the wheel. Due to the wheel’s inherent surface reflectivity, laser data collection can be affected by refraction, potentially impacting detection accuracy. This is an aspect that should be given special attention when consulting with wheel repair lathe manufacturers.
A significant concern for customers is whether the manufacturers of these wheel repair lathes offer support and training. Consider the availability of technical support and training provided by the manufacturer. Choose a reputable company that offers comprehensive support, including assistance with installation, training programs, and ongoing maintenance. It is crucial to inquire about the available forms of after-sales support and training provided by the CNC alloy wheel lathe manufacturer. Understand how they address and resolve issues that may arise. These are key aspects to consider. Will there be detailed video tutorials, written guides, or a range of support options such as face-to-face meetings, phone support, and video support? Some manufacturers may not provide adequate after-sales support once the CNC alloy wheel lathe is sold, which is a significant concern. This situation often occurs when customers choose manufacturers solely based on low prices, so it is important to consider multiple factors when making a decision.
The customer’s budget is also an important consideration: determine the budget for purchasing the lathe. While finding a lathe that meets your requirements is crucial, it is essential to balance budget constraints with the quality and functionality you need. Choosing a manufacturer that offers high-quality configurations within your financial means is paramount. This is often directly linked to the price. Pursuing a low price often carries significant risks in terms of quality, user experience, and after-sales service. Therefore, we encourage you to consider multiple factors and select a CNC alloy wheel lathe that fits your budget. Generally, price and quality are directly proportional.
If you encounter difficulties in selecting a CNC alloy wheel lathe, another effective way is to use reviews and recommendations as a reference. Read customer reviews, recommendations, and seek advice from professionals in the alloy wheel repair industry. Their insights can provide valuable information about the reliability, performance, and suitability of different lathe models. Reviews related to CNC alloy wheel lathes generally tend to be practical. You can find information about the pros and cons of the specific wheel lathe in these reviews. However, it is important to carefully consider these reviews, as some may be deliberately biased positive or negative reviews from customers. Recommendations from friends can also be reliable, especially if they have personal experience using or encountering similar CNC alloy wheel repair lathes, although they may earn a commission. It is still important to assess and evaluate independently.
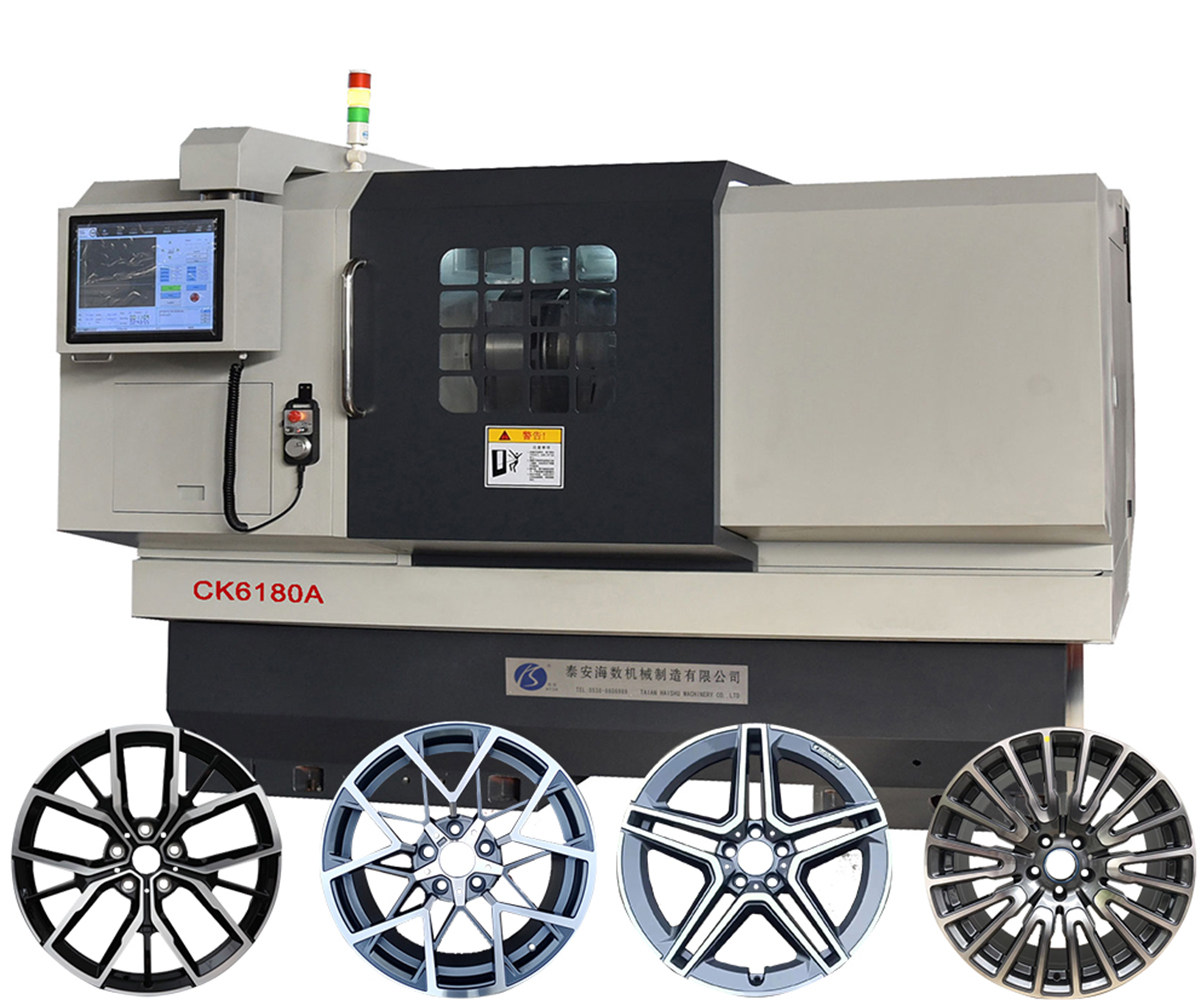
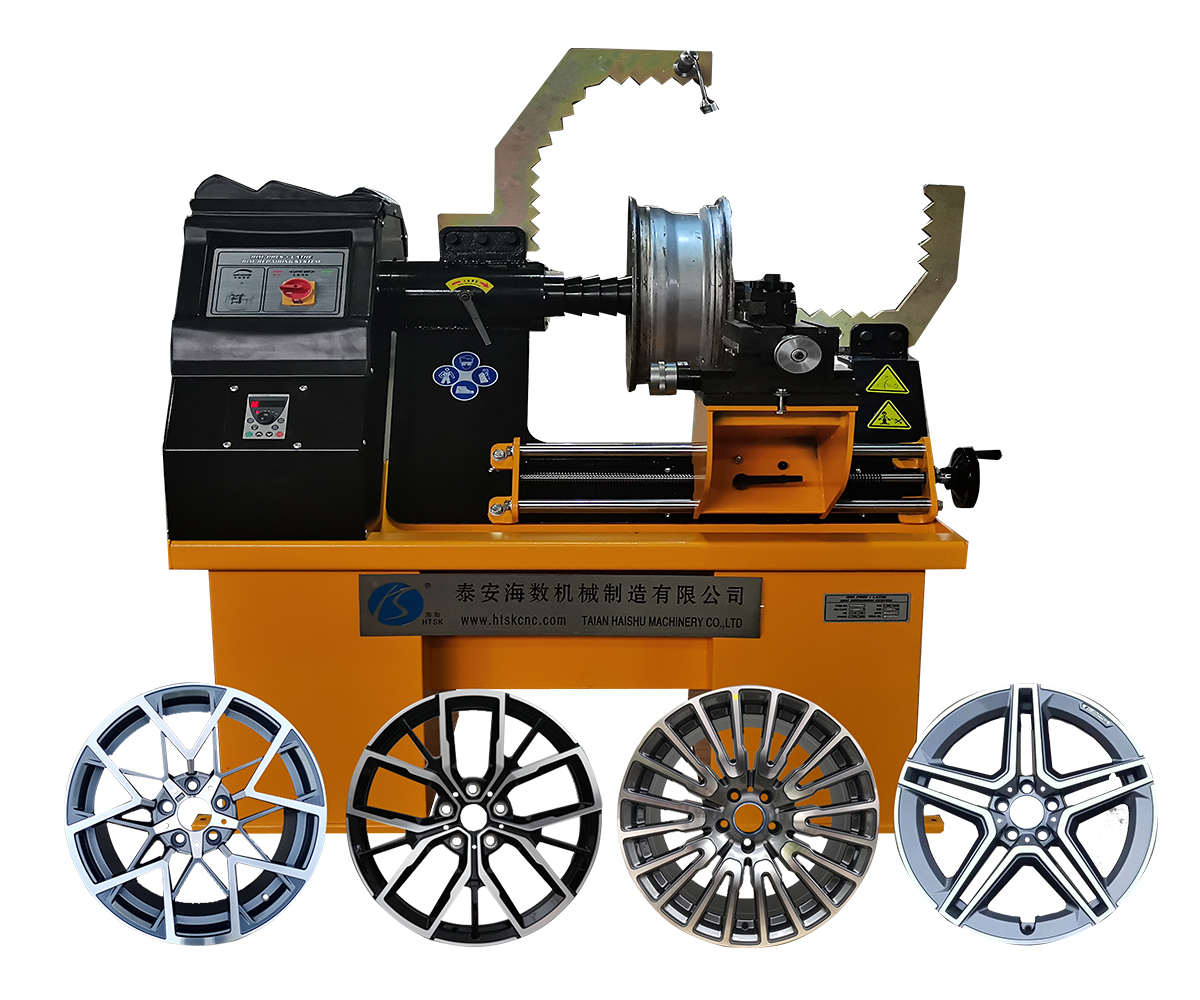
Why can we provide you with such professional information? Because I am a professional manufacturer specializing in the design, production, manufacturing, sales, and service of CNC alloy wheel lathe machines. We have a wide customer base worldwide. Our production of wheel repair lathes has evolved and expanded in scale and models based on different customer requirements. We fully consider market demands and manufacture CNC alloy wheel lathe machines in various models, structures, and configurations. We take a comprehensive approach to factors such as the size, model structure, system, precision, customer budget, market feedback, and after-sales service of wheel repair lathes. Therefore, when choosing TAIAN HAISHU Machinery Co., Ltd., you can confidently make your purchase. We also make every effort to provide you with customized wheel repair lathe machines. You are welcome to visit our company or contact us via email.