1. How to Perform CNC Alloy Wheel Repair
Modern CNC alloy wheel repair is a new method for refurbishing automotive aluminum alloy wheels. It utilizes specialized CNC wheel repair lathes, wheel repair machines, and alloy wheel lathes for automated restoration. So, what exactly is the process of CNC alloy wheel repair? Let’s introduce Taian Haishu’s CNC wheel repair machines to demonstrate the standard procedure for CNC alloy wheel repair.
2. Basic CNC Alloy Wheel Repair System
2.1 Introduction to the System
Taian Haishu’s independently developed CNC repair system incorporates numerous customer demands and functional designs. This system ensures high precision and efficiency in alloy wheel repair.
2.2 Key Features
Key features include one-key probing, which encompasses laser probing, touch probe detection, and Taian Haishu’s unique tool tip detection. These features streamline the repair process and improve accuracy.
2.3 Market Compatibility
This system can handle 99% of the wheel curvatures in the market, enabling customers to achieve one-click foolproof probing programs. This compatibility makes it a versatile solution for various wheel repair needs.
2.4 One-Click Probing Programs
The one-click probing programs simplify the repair process, allowing users to quickly and accurately set up their CNC wheel CNC machine. This feature is particularly beneficial for reducing setup time and increasing productivity.
3. One-Key Program Output in CNC Alloy Wheel Repair
3.1 Traditional Challenges
Traditional alloy wheel repair involves complex manual programming for CNC machining, requiring high technical skills from operators. This often leads to increased labor costs and potential for human error.
3.2 Haishu’s Solution
Haishu’s one-key program output perfectly addresses the high labor cost issue associated with technical expertise. By using one-key optimization or manual optimization, the system can directly output CNC programs without requiring a background in CNC programming.
3.3 Simplifying CNC Programming
The user-friendly interface makes it accessible for operators of all skill levels. This feature significantly reduces the technical cost for employers, making the process more economical and accessible.
3.4 Precision and Accuracy
Despite the simplified process, the system maintains high precision and accuracy in repairs. This ensures that the quality of the alloy wheel repair meets or exceeds industry standards.
4. One-Key Tool Setting in CNC Alloy Wheel Repair
4.1 Traditional Tool Setting
Previously, technical workers needed to input complicated machine coordinates for memory. This process was time-consuming and prone to errors, leading to inefficiencies and increased costs.
4.2 Haishu’s Innovation
With Haishu’s wheel repair system, a single button press sets the machining start coordinates for the tool. This innovation eliminates manual input, saving time and reducing costs.
4.3 Time-Saving
The one-key tool setting feature is easy to use, even for less experienced operators. This feature enhances productivity by reducing setup time and minimizing the potential for errors.
4.4 Accuracy
The system ensures high accuracy in setting tool coordinates, minimizing errors. This precision is crucial for achieving high-quality repairs and maintaining the integrity of the wheels.
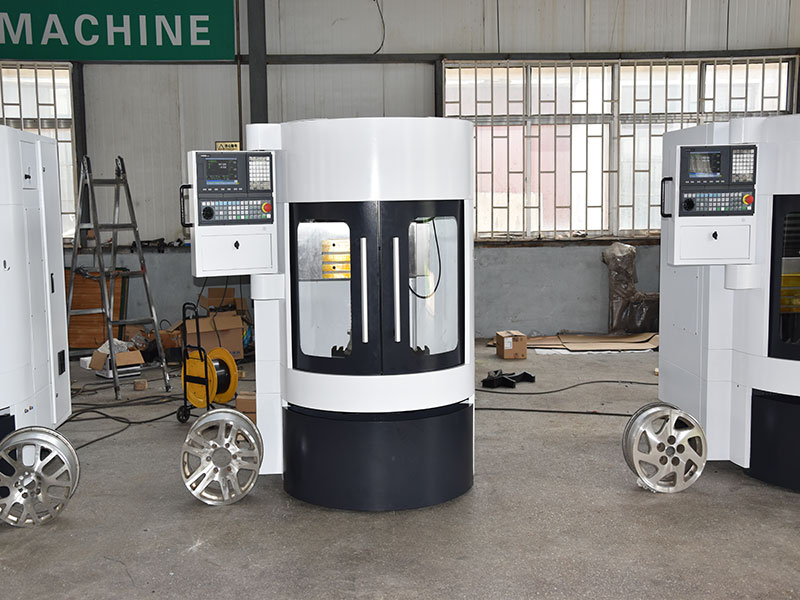
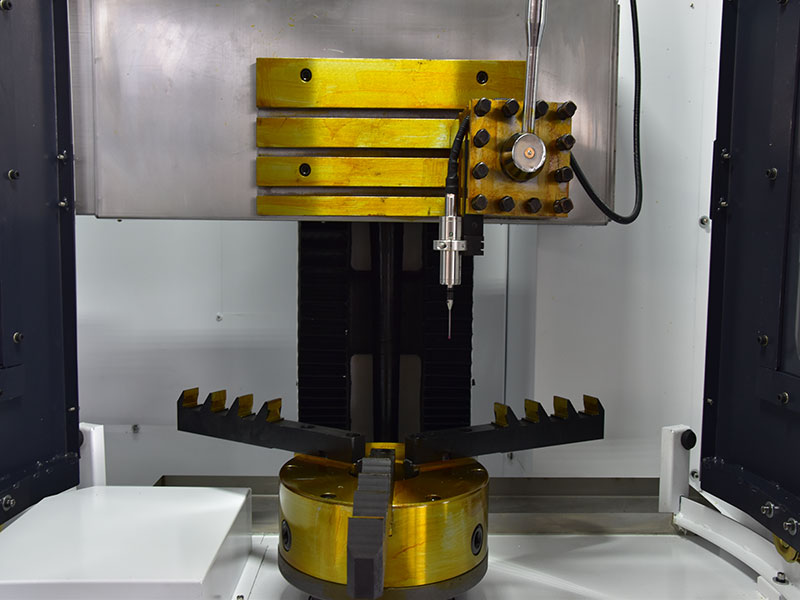
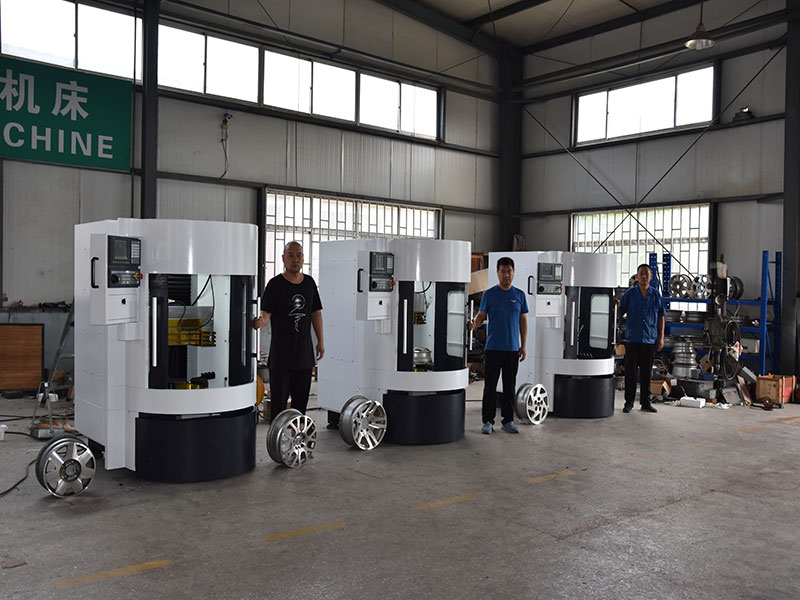
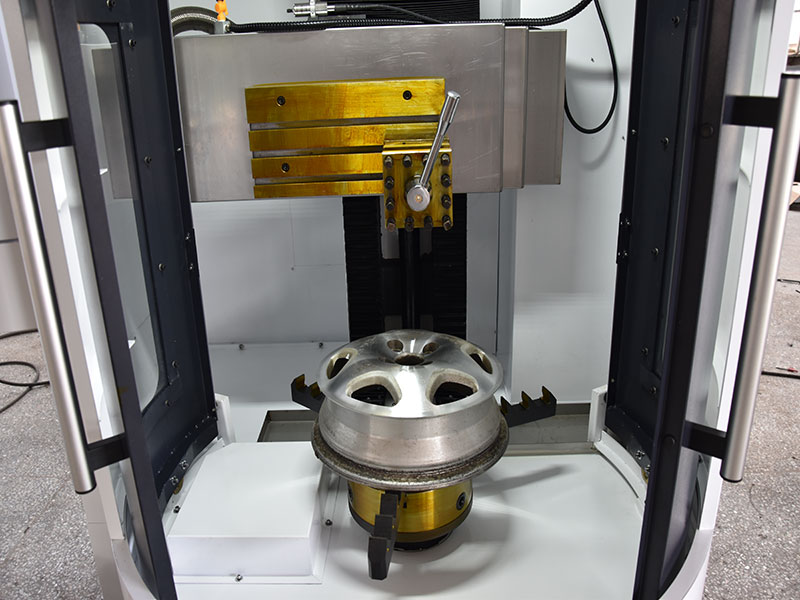
5. CNC Tool Processing in Alloy Wheel Repair
5.1 Importance of CNC Tools
CNC alloy wheel repair naturally involves CNC tool processing. The quality of the tools used in the repair process directly impacts the outcome of the repairs.
5.2 Material Quality
Taian Haishu uses imported diamond tools to achieve precise cutting. These high-quality tools ensure that the repaired wheels meet the highest standards of quality and durability.
5.3 Surface Finish
These tools enhance the surface finish of the repaired wheel, meeting high customer standards. This is especially suitable for customers aiming for mirror finishes or brushed effects.
5.4 Durability
The high-quality materials used in the tools ensure durability and long life. This reduces the need for frequent tool replacements, lowering overall maintenance costs.
6. Hardware Configuration for CNC Alloy Wheel Repair
6.1 Tool Post Options
Taian Haishu provides a straight-line tool post, reducing maintenance costs and failure rates. This configuration simplifies tool and probe clamping, making the process more efficient.
6.2 Simplified Clamping
Additionally, they offer manual or electric four-position tool posts for tool rotation. Though these are costlier and more complex to maintain, they offer greater flexibility for various repair tasks.
6.3 Primary Choice
The straight-line tool post remains the primary choice for users due to its simplicity and reliability. Reduced maintenance needs translate to lower long-term costs for users.
6.4 Maintenance
By reducing the time and skill required, this feature also reduces operational costs. User preferences generally lean towards configurations that offer the best balance of cost and functionality.
7. Guide Rail Options for CNC Alloy Wheel Repair
7.1 Hard Rails
Haishu offers multiple choices for guide rails, including hard rails. These are suitable for smaller wheels with lower surface finish demands.
7.2 Linear Guide Rails
Linear guide rails are available to meet various price and functional requirements. For higher demands on movement speed, surface finish, and precision, linear guide rails are recommended.
7.3 Transmission Types
Linear guide rails are available with ball or roller transmissions to meet precision and surface finish requirements. These options allow customers to choose the best configuration for their specific needs.
7.4 Performance
Each type of guide rail offers distinct performance benefits, ensuring optimal results for different applications. Future developments in guide rail technology will likely enhance performance and durability further.
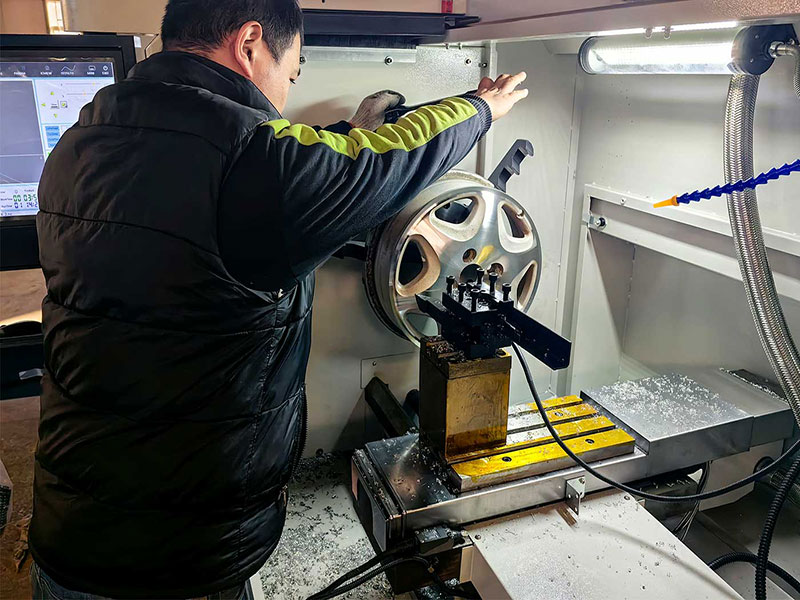
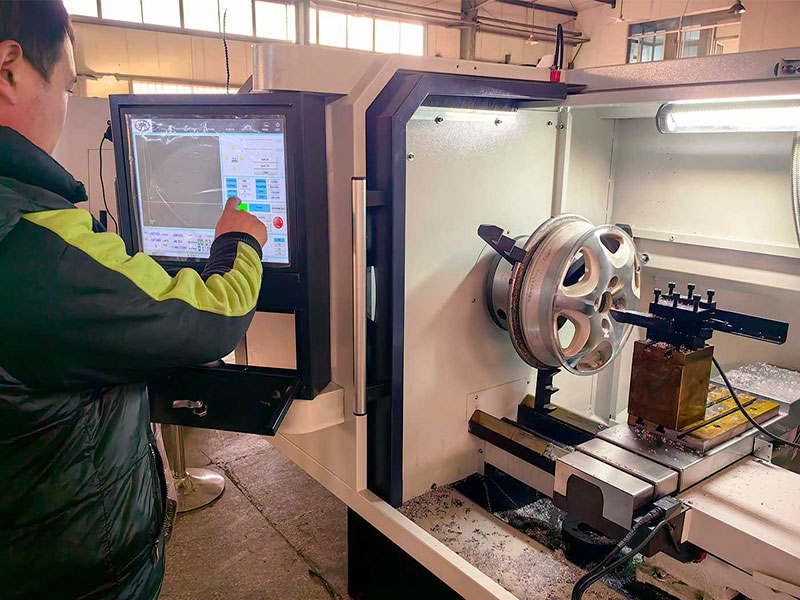
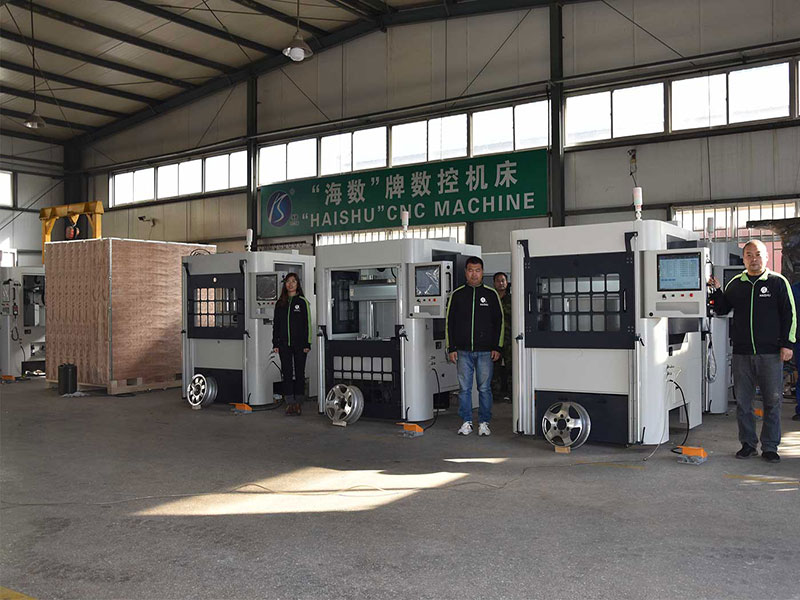
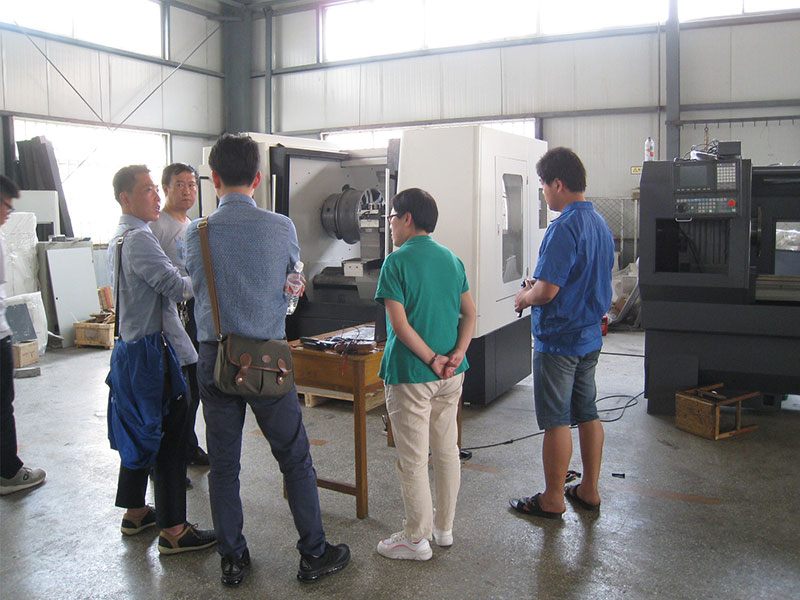
8. Machine Bed Structure for CNC Alloy Wheel Repair
8.1 Bed Structure Options
Taian Haishu also provides diverse options in machine bed structures, including standard horizontal wheel repair lathes and vertical wheel repair lathes. This variety ensures that customers can find the right machine for their specific repair needs.
8.2 Horizontal Wheel Repair Lathes
For wheels up to 21 inches, a horizontal wheel lathe is suitable as smaller wheels do not cause significant vibrations. This option is ideal for smaller repair shops or mobile services.
8.3 Vertical Wheel Repair Lathes
For wheels between 16-26 inches, a vertical wheel repair lathe is ideal, effectively counteracting centrifugal forces. These lathes offer stability and precision for larger wheel repairs.
8.4 Mobile Wheel Repair Machines
To offer on-site service, Haishu has developed mobile wheel repair machines. These machines are designed for convenience and flexibility, allowing repairs to be performed at the customer’s location.
8.5 Size Considerations
Vertical wheel repair lathes can support wheels up to 35 inches. Haishu offers customization options to meet specific customer needs and preferences, ensuring that their machines can handle a wide range of repair tasks.
9. Conclusion on CNC Alloy Wheel Repair
9.1 Summary
This is a brief introduction to Taian Haishu’s CNC alloy wheel repair. The advanced features and high-quality components of their wheel repair machines make them a leading choice for automotive wheel refurbishment.
9.2 Feedback
If you have more ideas or suggestions, please let me know; I am happy to answer your questions. Customer feedback is invaluable in helping us improve our products and services.
9.3 Custom Solutions
We also support customized solutions for our clients. With many agents and partners globally, if you wish to join us, please contact me.
9.4 Global Presence
Our global presence ensures that we can provide support and services to clients around the world. We are committed to helping our customers achieve the best possible results with their wheel repairs.
9.5 Future Prospects
Future prospects for CNC alloy wheel repair look promising, with continued advancements and innovations. We are excited to be at the forefront of this evolving industry.
9.6 Customer Benefits
Customers benefit from reduced costs, increased efficiency, and higher quality repairs. Our machines are designed to deliver consistent, high-quality results, making us a trusted partner in the wheel repair industry.
9.7 Join Us
We invite you to join us in revolutionizing the wheel repair industry with cutting-edge technology. Our commitment to innovation and customer satisfaction sets us apart from the competition.
9.8 Contact Information
For more information or to become a partner, please contact us. We look forward to working with you and helping you achieve your wheel repair goals.