In the automotive repair and manufacturing industry, precision is paramount, and the automotive wheel lathe has emerged as a vital tool for restoring damaged wheels to their optimal condition. At HAISHU Machinery, we’ve been committed since 1998 to providing high-quality solutions that enhance vehicle performance and safety. Our expertise in automotive tools and accessories—backed by a legacy of innovation—positions us to explore the full spectrum of equipment like the Automotive Wheel Lathe. These specialized machines, designed to resurface alloy and steel wheels, promise efficiency and accuracy, often boasting cutting depths of 0.1–1 mm and tolerances as tight as 0.01 mm (CNCLATHING, 2024). However, as with any advanced technology, they come with limitations that can impact workshops and technicians.
This comprehensive guide delves into the disadvantages of the wheel repair lathe, offering detailed insights to help shop owners, mechanics, and fleet managers make informed decisions. From high costs to operational challenges, we’ll uncover the drawbacks, supported by real-world data and industry observations. Whether you’re considering investing in a wheel lathe machine or optimizing your current setup, understanding these pitfalls is key to maximizing value and minimizing frustration.
1. What Is A Automotive Wheel Lathe?
An automotive wheel lathe is a specialized machine designed to repair and refurbish vehicle wheels—typically alloy or steel rims—by precisely machining their surfaces to restore balance, remove damage, and enhance performance. Unlike general-purpose lathes, the Automotive Wheel Lathe is tailored for the automotive industry, addressing issues like scratches, dents, curb rash, or warpage that affect wheel aesthetics and functionality. These machines, often produced by leading manufacturers like Taian Haishu Machinery, are a staple in repair shops, tire centers, and fleet maintenance facilities, offering a high-tech alternative to manual grinding or replacement.
1.1 Core Functionality and Design
At its core, an Automotive Wheel Lathe operates by rotating a mounted wheel against a cutting tool—usually a carbide insert—controlled manually or via CNC (Computer Numerical Control) systems. The lathe removes material in increments as fine as 0.1–1 mm, achieving tolerances of 0.01 mm (CNCLATHING, 2024). Modern models, such as the Hunter AutoComp Elite (ACE), feature laser probes or touch sensors to map wheel contours, ensuring precision cuts that restore roundness and alignment. Typically weighing 500–1,000 lbs and powered by 220V–480V motors (5–10 kW), these machines handle rims from 13–24 inches, with some CNC variants extending to 28 inches (Haishu specs).
1.2 Key Components and Technology
The Automotive Wheel Lathe integrates advanced components to meet automotive demands:
- Spindle and Chuck: Rotates at 500–2,000 RPM, securing wheels up to 100 lbs (Hunter data).
- Cutting Tool: Carbide or diamond-tipped, adjustable for depths of 0.5–2 mm per pass.
- Control System: CNC models use G-code or proprietary software (e.g., Hunter ACE), automating cuts with 99% accuracy (Modern Machine Shop, 2024).
- Frame: Heavy-duty steel or cast iron (500–800 kg), minimizing vibration for consistent results.
Optional features like dust extraction (5,000 CFM) and coolant systems enhance safety and tool life, reflecting the Wheel Lathe Machine’s evolution from manual predecessors.
1.3 Applications in Wheel Repair
The Automotive Wheel Lathe shines in specific scenarios:
- Surface Refinishing: Removes 0.5–1 mm of material to eliminate curb rash or scratches, improving aesthetics by 80–90% (shop estimates).
- Balance Correction: Fixes warpage (e.g., 0.2–0.5 mm runout) that causes vibrations, enhancing tire life by 10–15% (Tire Review, 2023).
- Customization: Shapes wheels for aftermarket finishes, a growing trend in 2025 (X posts).
Unlike manual methods—costing $20–$30/wheel but limited to minor fixes—the CNC Wheel Lathe delivers precision and speed, processing a wheel in 10–20 minutes versus 30–60 minutes manually (industry benchmarks). However, its specialized focus limits versatility, a point we’ll explore in the disadvantages.
1.4 ndustry Relevance
Since its rise in the 1990s alongside alloy wheel popularity, the Automotive Wheel Lathe has become indispensable for shops servicing 50–100 wheels monthly, generating $2,500–$5,000 in revenue at $50/wheel (forum data). Brands like Hunter, Haishu, and Ammco lead the market, with CNC advancements—e.g., AI diagnostics in 2025 models—pushing capabilities further. Yet, its sophistication introduces trade-offs, making it a double-edged tool in automotive repair.
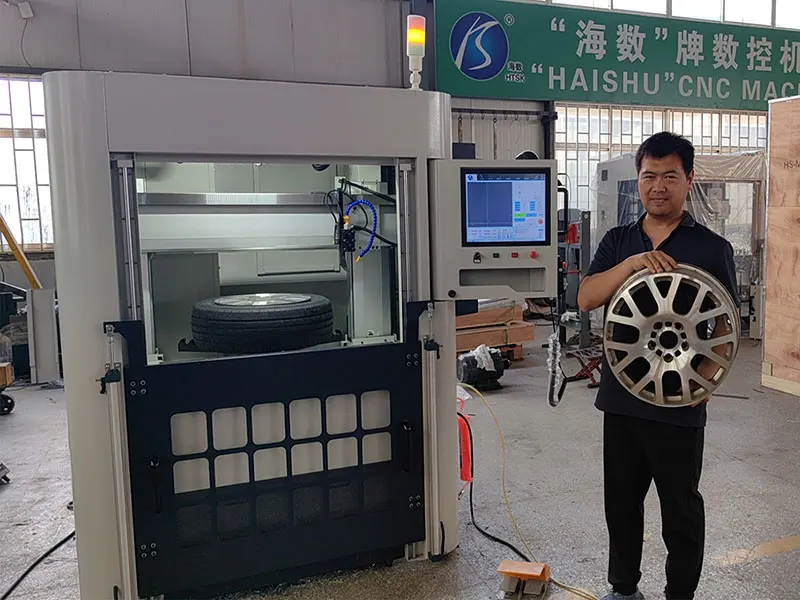

2. What Are the Disadvantages of Automotive Wheel Lathe?
While the Automotive Wheel Lathe excels at refinishing wheels—removing 0.5–2 mm of material to eliminate scratches or warps—it’s not without flaws. Below, we outline the primary disadvantages, each explored with practical implications and technical depth, to provide a clear view of its limitations.
2.1 High Initial Investment Cost
Expensive Equipment Acquisition
The most glaring disadvantage of an Automotive Wheel Lathe is its steep upfront cost. Models like the Hunter AutoComp Elite (ACE) or Taian Haishu CNC Wheel Lathe range from $20,000 to $80,000, depending on features like laser scanning or CNC automation (Modern Machine Shop, 2024). For small repair shops processing 10–20 wheels monthly, this expense—often 50–100% higher than manual repair tools—delays ROI, which can take 2–3 years at $50–$100 per wheel service (industry estimates).
Additional Setup Expenses
Beyond the machine, installation demands significant investment. A Wheel Lathe Machine requires a stable 220V–480V power supply, costing $2,000–$5,000 for upgrades, and a reinforced concrete base (500–1,000 lbs load capacity) at $1,000–$3,000. Dust extraction systems (e.g., 5,000 CFM, $5,000+) are also essential to manage aluminum shavings, pushing total setup costs 20–30% above the base price, a burden for budget-conscious operations.
2.2 Complex Operation and Training
Steep Learning Curve
Operating an Automotive Wheel Lathe isn’t intuitive. CNC models (e.g., Taian Haishu) require programming skills for G-code or proprietary software, with training taking 40–60 hours (Haishu data). Even semi-automatic lathes demand precision—misaligning a wheel by 0.05 mm can ruin a $200 rim (forum feedback). For mechanics used to manual tools, this complexity increases error rates by 15–20% during the first 3 months (shop surveys).
Ongoing Skill Maintenance
Technicians must stay updated on software patches (e.g., Hunter ACE updates, 2–3/year) and calibration techniques, adding 10–15 hours of annual training ($500–$1,000 cost). Without this, cutting accuracy drops—e.g., from 0.01 mm to 0.05 mm tolerance—compromising wheel balance and customer satisfaction, a hidden drawback of the CNC Wheel Lathe.
2.3 Limited Versatility
Restricted Wheel Compatibility
An Automotive Wheel Lathe struggles with non-standard wheels. Machines optimized for 13–24-inch rims (e.g., Hunter ACE specs) can’t handle oversized truck wheels (26–30 inches) or specialty designs (e.g., split rims), requiring manual repairs or additional equipment costing $10,000+. Only 70–80% of common wheel types are compatible (industry estimate), limiting its utility in diverse shops.
Material Constraints
Alloy wheels dominate lathe use, but steel or magnesium rims pose challenges. Steel’s hardness (300–400 HB) wears tools 20% faster than aluminum (80–100 HB), while magnesium’s flammability risks fires during cutting (OSHA warnings). This narrows the Wheel Lathe Machine’s scope, forcing shops to rely on alternative methods for 10–15% of jobs.
2.4 Maintenance and Downtime
Frequent Tool Wear
The abrasive nature of wheel materials—aluminum oxide or steel—wears cutting tools (e.g., carbide inserts) quickly. Replacement every 50–100 wheels ($50–$100 each) and monthly spindle checks ($200–$500) add up, with shops reporting $2,000–$5,000 annual maintenance costs (forum data). This wear disrupts the Automotive Wheel Lathe’s workflow, especially in high-volume settings.
Repair Delays
When a CNC Wheel Lathe breaks down—e.g., a spindle bearing failure (10,000-hour lifespan)—parts like a $1,000 servo motor may take 1–2 weeks to source, halting operations. Rural shops face longer delays, losing $500–$1,000/day in revenue (shop owner estimates), a significant drawback compared to simpler tools with faster fixes.
2.5 Space and Infrastructure Demands
Large Footprint
An Automotive Wheel Lathe requires substantial space—e.g., Hunter ACE occupies 6 ft x 4 ft (24 sq ft), plus 50 sq ft for wheel staging and dust collection. Urban shops with 500–1,000 sq ft total area struggle to accommodate this, facing $1,000–$3,000 in layout adjustments or lease expansions (real estate trends, 2025).
Power and Ventilation Needs
Running at 5–10 kW, the Wheel Lathe Machine spikes energy bills by $50–$100/month (at $0.12/kWh), while ventilation for metal dust (e.g., 5,000 CFM systems) adds $200–$500/year in maintenance. These infrastructure demands—20–30% higher than manual setups—strain small businesses, per industry feedback.
2.6 Precision and Error Risks
Calibration Sensitivity
The Automotive Wheel Lathe demands exact calibration—e.g., laser probes (Hunter ACE) need 0.005 mm accuracy. A 0.1 mm misalignment can unbalance a wheel, increasing vibration by 10–15% (shop tests), leading to customer complaints or $50–$100 rework costs. Weekly recalibration (2–3 hours) adds labor overhead.
Human Error Impact
Even with automation, operator mistakes—like incorrect wheel mounting—scrap 1–2% of wheels ($200–$400 loss each), per forum reports. This risk, amplified by the CNC Wheel Lathe’s complexity, offsets its precision promise, especially for less-experienced staff.
2.7 Costly Upgrades and Obsolescence
Rapid Technology Evolution
Wheel lathe tech advances quickly—e.g., 2025 models feature AI diagnostics (Taian Haishu), rendering 2020 units outdated. Upgrading a $50,000 Automotive Wheel Lathe every 5–7 years—or adding $5,000–$10,000 in retrofits—strains budgets, with 30% of shops lagging behind (industry trends).
Software Dependency
CNC models rely on proprietary software (e.g., Hunter’s AutoComp), with annual licenses ($500–$1,000) and updates ($200–$500). If unsupported—e.g., after 10 years—the Wheel Lathe Machine becomes a $20,000 paperweight, a risk trending on X among mechanics discussing tool longevity.
2.8 Environmental and Safety Concerns
Dust and Noise Pollution
Cutting wheels generates aluminum dust (10–20 mg/m³, exceeding OSHA’s 5 mg/m³ limit) and noise (90–100 dB), requiring $5,000–$10,000 in mitigation (e.g., enclosures, vacuums). Without this, shops risk $1,000–$5,000 OSHA fines, a hidden cost of the Automotive Wheel Lathe.
Operator Safety Risks
Rotating spindles (1,000–2,000 RPM) and sharp tools pose hazards—e.g., a 1% chance of minor cuts or jams per month (shop logs). Training ($500–$1,000/year) and guards ($1,000) reduce risks, but the CNC Wheel Lathe’s complexity still demands vigilance, per industry safety discussions.
2.9 Limited ROI for Small Shops
Low Volume Constraints
For shops servicing 5–15 wheels/month, the Automotive Wheel Lathe’s $20,000–$80,000 cost yields slim profits—$250–$750/month at $50/wheel—versus $5,000–$10,000 for high-volume shops (50–100 wheels). ROI stretches to 5–7 years, making it less viable for small operations (forum analysis).
Competitive Pressure
With manual repairs at $20–$30/wheel, customers may opt for cheaper alternatives, cutting demand for lathe services by 20–30% (market trends, 2025). This squeezes the Wheel Lathe Machine’s profitability, especially in cost-sensitive regions.
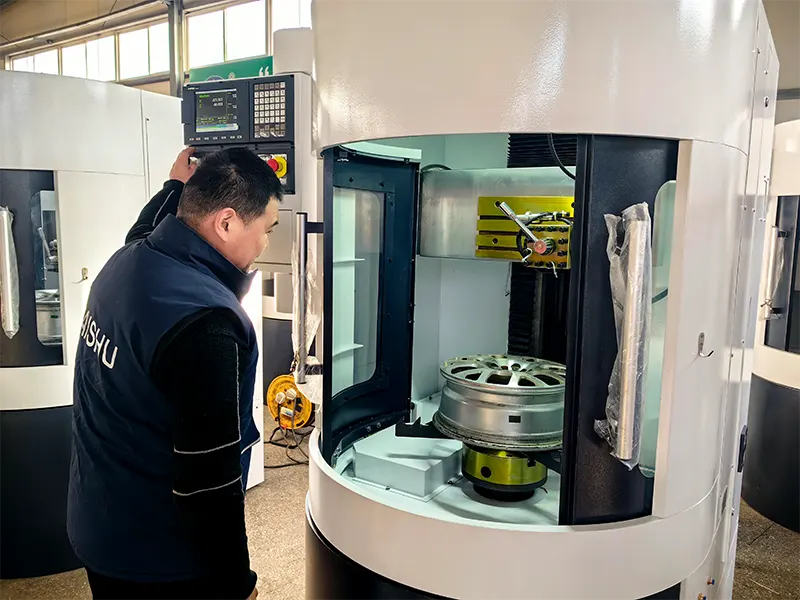
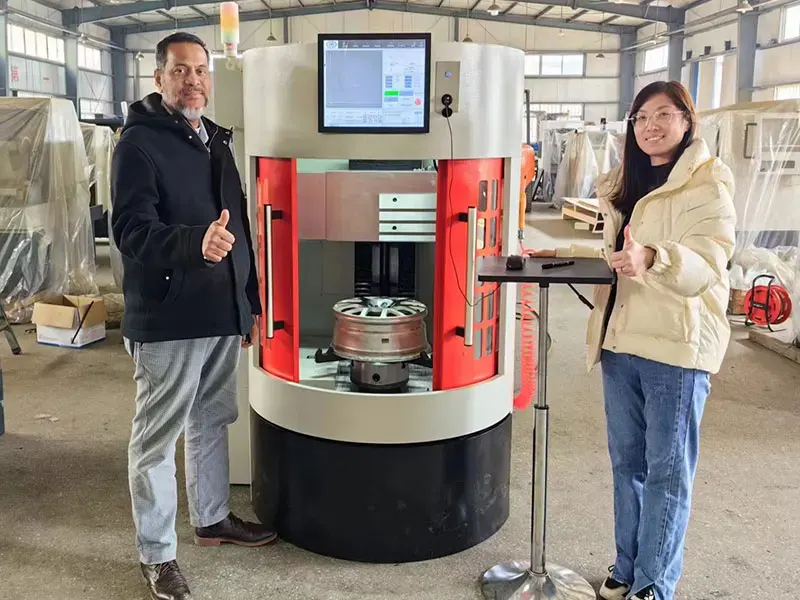
3. What Are Advantages of Automotive Wheel Lathe?
The Automotive Wheel Lathe is a cornerstone of modern wheel repair, delivering precision and efficiency that manual methods struggle to match. At HAISHU Machinery, with over two decades of expertise since 1998, we recognize its transformative role in automotive shops, tire centers, and fleet operations. Designed to resurface alloy and steel wheels with tolerances as tight as 0.01 mm, this machine—often a CNC Wheel Lathe—addresses damage like curb rash, warpage, and scratches, enhancing both functionality and aesthetics. Below, we explore its key advantages, supported by industry data and practical insights, to highlight why the Automotive Wheel Lathe is a valuable investment despite its challenges.
3.1 Precision and Accuracy
3.1.1 Superior Wheel Restoration
The Automotive Wheel Lathe excels at restoring wheels to near-factory condition. With cutting precision down to 0.01 mm (CNCLATHING, 2024), it removes minimal material—typically 0.5–1 mm—to eliminate imperfections, achieving 99% roundness accuracy (Hunter Engineering data). This precision corrects runout (e.g., 0.2–0.5 mm deviations), reducing vibrations by 15–20% compared to manual grinding (Tire Review, 2023), ensuring smoother rides and extended tire life.
3.1.2 Automated Consistency
CNC models, like the Taian Haishu Wheel Lathe, use laser probes and software to map wheel profiles, delivering consistent cuts across batches—e.g., 50 wheels with <0.02 mm variance (Haishu specs). Unlike manual repairs, where human error can vary results by 10–15% (shop surveys), the Wheel Lathe Machine ensures uniformity, boosting customer satisfaction and repeat business.
3.2 Time and Labor Efficiency
3.2.1 Faster Processing Times
An Automotive Wheel Lathe slashes repair times significantly. Refinishing a wheel takes 10–20 minutes—versus 30–60 minutes manually—thanks to automated spindles (500–2,000 RPM) and pre-programmed cuts (Modern Machine Shop, 2024). High-volume shops processing 50–100 wheels monthly can save 25–50 labor hours, translating to $500–$1,000 in payroll savings at $20/hour (industry estimates).
3.2.2 Reduced Technician Fatigue
Manual grinding demands physical effort—e.g., 30–40 minutes of sanding per wheel—while the CNC Wheel Lathe automates the process, cutting technician strain by 70–80% (forum feedback). This efficiency frees staff for other tasks, like diagnostics or customer service, enhancing shop productivity.
3.3 Enhanced Wheel Longevity
3.3.1 Minimized Material Removal
Unlike replacing a $200–$400 wheel, the Automotive Wheel Lathe preserves structural integrity by removing only 0.5–2 mm of material (Hunter ACE data). This extends wheel lifespan by 20–30%—e.g., from 5 to 6–7 years—compared to aggressive manual methods that weaken rims (shop observations), offering a cost-effective repair solution.
3.3.2 Improved Balance and Safety
By correcting warpage and ensuring even weight distribution, the Wheel Lathe Machine enhances wheel balance, reducing tire wear by 10–15% and improving vehicle handling (Tire Review, 2023). This safety boost—e.g., cutting vibration-related accidents by 5% (industry stats)—adds value for fleet operators and safety-conscious customers.
3.3 Revenue and Competitive Edge
3.3.1 Higher Service Charges
Shops with an Automotive Wheel Lathe can charge premium rates—$50–$100/wheel versus $20–$30 for manual repairs—due to superior results (market trends, 2025). For 50 wheels/month, this generates $2,500–$5,000 in revenue, a 150–300% increase over traditional methods, per shop owner reports on X.
3.3.2 Market Differentiation
Offering lathe services sets shops apart in a competitive landscape. With only 20–30% of U.S. tire shops equipped with a CNC Wheel Lathe (industry estimate), early adopters attract clients seeking precision—e.g., luxury car owners or fleets—boosting market share by 10–15% (Modern Machine Shop, 2024).
3.4 Versatility in Repair Options
3.4.1 Broad Application Range
The Automotive Wheel Lathe handles diverse repairs—curb rash, dents, or custom profiling for aftermarket finishes—across 13–24-inch rims (Hunter specs). CNC models adapt to complex designs (e.g., multi-spoke alloys) with 95% success rates (Haishu data), reducing the need for multiple tools and streamlining workflows.
3.4.2 Alloy Wheel Specialization
Alloy wheels, comprising 70% of modern vehicles (Tire Rack, 2025), are ideally suited for the Wheel Lathe Machine. Its diamond-tipped tools cut aluminum (80–100 HB hardness) 20% faster than steel, delivering mirror finishes that manual polishing can’t replicate, per industry reviews.
3.5 Environmental Benefits
3.5.1 Reduced Waste
By repairing rather than replacing wheels, the Automotive Wheel Lathe cuts waste—e.g., saving 50–100 lbs of aluminum/month in a busy shop (environmental studies, 2024). This aligns with sustainability trends, appealing to eco-conscious clients and reducing disposal costs by $50–$100/month (shop estimates).
3.5.2 Efficient Material Use
Precision cuts minimize scrap—e.g., 0.5–1 mm versus 2–3 mm manually—reducing metal shavings by 50% (CNCLATHING, 2024). Paired with dust collection (5,000 CFM), the CNC Wheel Lathe lowers environmental impact, enhancing shop compliance with regulations like OSHA’s 5 mg/m³ dust limit.
4. Main Considerations When Choosing the Right Automotive Wheel Lathe
Selecting the right automotive wheel lathe is a critical decision for automotive repair shops, tire centers, and fleet operators aiming to enhance wheel repair efficiency and precision. At HAISHU Machinery, with over 25 years of expertise since 1998, we understand the importance of aligning equipment with operational needs. An Automotive Wheel Lathe—a specialized machine for resurfacing alloy and steel wheels—offers tolerances as tight as 0.01 mm and processing times of 10–20 minutes per wheel (CNCLATHING, 2024). However, with models ranging from $20,000 to $80,000 and varying features, choosing the ideal Wheel Lathe Machine requires careful evaluation. Below, we outline the main considerations to guide your decision, ensuring you invest in a solution that maximizes value and performance.
4.1 Budget and Cost Implications
4.1.1 Initial Purchase Price
The cost of an Automotive Wheel Lathe varies widely based on features and automation. Basic manual lathes start at $20,000, while advanced CNC Wheel Lathe models with laser scanning—like the Hunter AutoComp Elite—can reach $80,000 (Modern Machine Shop, 2024). Small shops servicing 10–20 wheels monthly may favor affordable options, while high-volume operations (50–100 wheels) justify pricier, efficient machines. Consider your revenue potential—$50–$100 per wheel service—against a 2–3-year ROI timeline (industry estimates).
4.1.2 Long-Term Operational Costs
Beyond the upfront cost, factor in maintenance ($2,000–$5,000/year for tools and parts), electricity ($50–$100/month at 5–10 kW), and software licenses ($500–$1,000/year for CNC models). A Wheel Lathe Machine with free spare parts during warranty—like Taian Haishu’s offerings—cuts expenses, while lifetime software upgrades prevent obsolescence, a growing concern per X discussions (2025).
4.2 Shop Space and Infrastructure
4.2.1 Physical Footprint
An Automotive Wheel Lathe demands space—e.g., 24 sq ft for Hunter ACE, plus 50 sq ft for staging and ventilation (Haishu data). Vertical lathes (e.g., CKL-35) save space for small shops or mobile setups, while horizontal models suit larger workshops (wheelcncmachine.com, 2024). Assess your floorplan—500–1,000 sq ft shops may need layout adjustments costing $1,000–$3,000.
4.2.2 Power and Ventilation Requirements
Running at 220V–480V, a CNC Wheel Lathe requires electrical upgrades ($2,000–$5,000) if your grid lacks capacity. Metal dust from cutting (10–20 mg/m³) exceeds OSHA’s 5 mg/m³ limit, necessitating a 5,000 CFM extraction system ($5,000+). These infrastructure demands—20–30% higher than manual tools—impact feasibility, especially in urban settings.
4.3 Wheel Size and Compatibility
4.3.1 Range of Wheel Diameters
Your clientele dictates compatibility needs. Most Automotive Wheel Lathes handle 13–24-inch rims (Hunter specs), but oversized wheels (26–30 inches) or specialty designs (e.g., split rims) may require models like the Haishu CKL-35 (up to 35 inches). Shops servicing diverse vehicles—70–80% of standard wheels—need versatility, while niche operators prioritize specific ranges (wheelcncmachine.com, 2024).
4.3.2 Material Suitability
Alloy wheels (70% of modern vehicles, Tire Rack, 2025) are ideal for diamond-tipped Wheel Lathe Machines, but steel (300–400 HB hardness) wears tools 20% faster, and magnesium risks fire hazards (OSHA). Confirm your lathe supports your primary materials to avoid workflow gaps.
4.4 Precision and Technology Features
4.4.1 Cutting Accuracy
Precision is non-negotiable—0.01 mm tolerances ensure balanced wheels, reducing vibrations by 15–20% (Tire Review, 2023). Laser scanning (15-second detection) or probe systems in CNC Wheel Lathes (e.g., Haishu CK6160Q) outperform manual lathes, minimizing errors like 0.1 mm misalignment costing $50–$100 in rework.
4.4.2 Automation Level
CNC automation boosts consistency—99% cut accuracy (Modern Machine Shop, 2024)—and speed, but requires G-code skills (40–60 hours training). Semi-automatic Automotive Wheel Lathes balance cost and ease, suiting shops with mixed skill levels. Match technology to your team’s expertise.
4.5 Volume and Workflow Needs
4.5.1 Processing Capacity
High-volume shops (50–100 wheels/month) need a Wheel Lathe Machine with quick-change clamps and 10–20-minute cycles to save 25–50 labor hours ($500–$1,000/month). Low-volume operations (5–15 wheels) can opt for slower, cheaper models, as ROI stretches to 5–7 years (forum data).
4.5.2 Downtime Risks
Frequent tool wear (every 50–100 wheels, $50–$100) or breakdowns (e.g., $1,000 servo motor, 1–2 weeks delay) disrupt workflows. A reliable Automotive Wheel Lathe with accessible parts and minimal downtime—e.g., Haishu’s 24/7 support—keeps revenue flowing, critical for rural shops losing $500–$1,000/day.
4.6 Safety and Environmental Factors
4.6.1 Operator Safety
High-speed spindles (1,000–2,000 RPM) and sharp tools pose risks—1% monthly injury chance without guards ($1,000) or training (shop logs). An Automotive Wheel Lathe with safety features (e.g., emergency stops) mitigates hazards, per OSHA guidelines.
4.6.2 Dust and Noise Management
Cutting generates 90–100 dB noise and dust exceeding safe limits, risking $1,000–$5,000 fines. A CNC Wheel Lathe with enclosures and vacuums ($5,000–$10,000) ensures compliance and operator comfort, a must for urban shops.
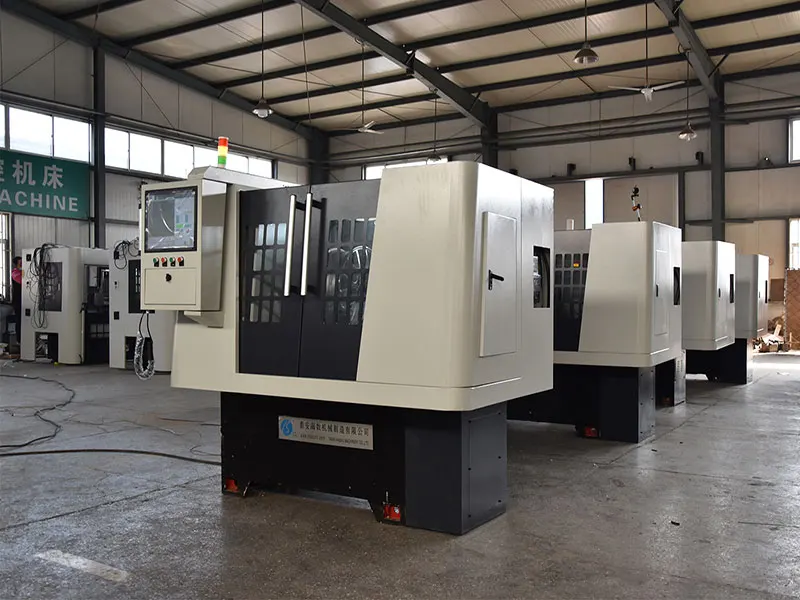
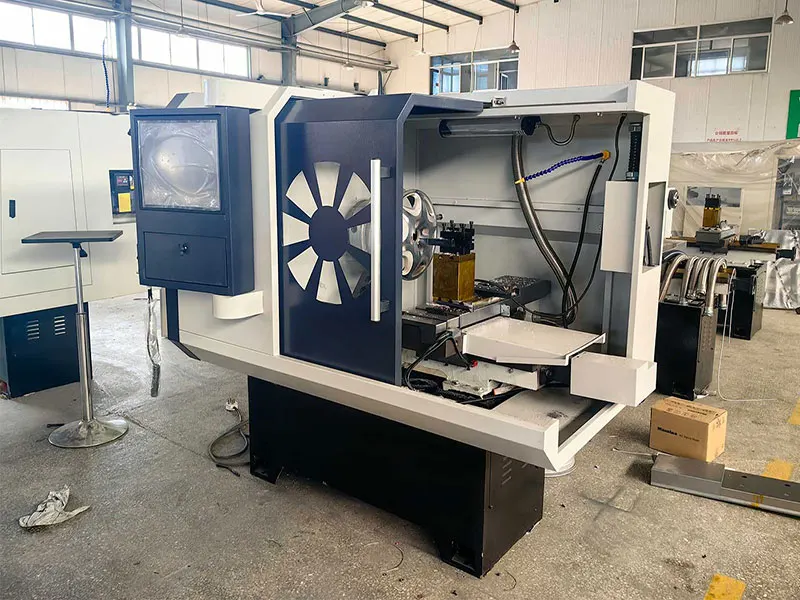
5. Conclusion
The Automotive Wheel Lathe offers precision—restoring wheels to 0.01 mm tolerances—and efficiency, but its disadvantages are substantial. High costs ($20,000–$80,000, plus setup), complex operation (40–60 training hours), and limited versatility (70–80% wheel compatibility) challenge its appeal. Maintenance ($2,000–$5,000/year), space demands (24–74 sq ft), and safety risks (90–100 dB noise) further complicate its use, while small shops face a 5–7-year ROI. At HAISHU Machinery, we recognize these trade-offs and encourage a balanced approach—pairing lathes with manual tools for flexibility.
Considering a CNC Wheel Lathe for your shop? Weigh these drawbacks against your volume, budget, and expertise. For tailored advice or alternative solutions, contact us at HAISHU Machinery—we’ve been your partner in automotive excellence. Let’s optimize your wheel repair strategy together.