1. What is an Alloy Repair Machine?
An alloy repair machine is a specialized device used for restoring small car aluminum alloy wheels that have been scratched or damaged due to scrapes or deformation. When customers consider purchasing a wheel CNC machine, they often have many questions and concerns about features and capabilities. Below, we will introduce Taian Haishu’s alloy repair machine, offering a reliable reference for those looking to invest in wheel repair equipment.
2. How Does an Alloy Repair Machine Work?
2.1 Initial Wheel Reshaping Process
If a customer’s car wheel is deformed, the first step is to correct and reshape it using a specialized wheel reshaping machine. This initial repair is crucial for ensuring the wheel can be restored to its original condition. The deformed wheel is clamped onto the machine and heated with a blowtorch to soften the aluminum material.
2.2 Hydraulic Jack Utilization
An automatic hydraulic jack equipped with a Taiwanese hydraulic valve is employed for the shaping process. The technician gradually corrects the wheel using the hydraulic jack, eliminating any deformation. This process can take approximately 30 minutes, depending on the severity of the damage. If the wheel cools during this time, it may need to be reheated to ensure effective reshaping.
3. What should you do if the alloy wheel cracks?
3.1 Aluminum Welding Treatment
In cases of severe impact, the alloy wheel may crack. This situation requires aluminum welding treatment before the wheel can be clamped onto the alloy repair machine for reshaping. The welding process is essential to restore the structural integrity of the wheel.
3.2 Cutting Tools for Precision
After reshaping, the wheel can be cut using tools provided by the wheel repair machine to meet factory standards. This step ensures that the wheel is not only visually appealing but also safe for use.
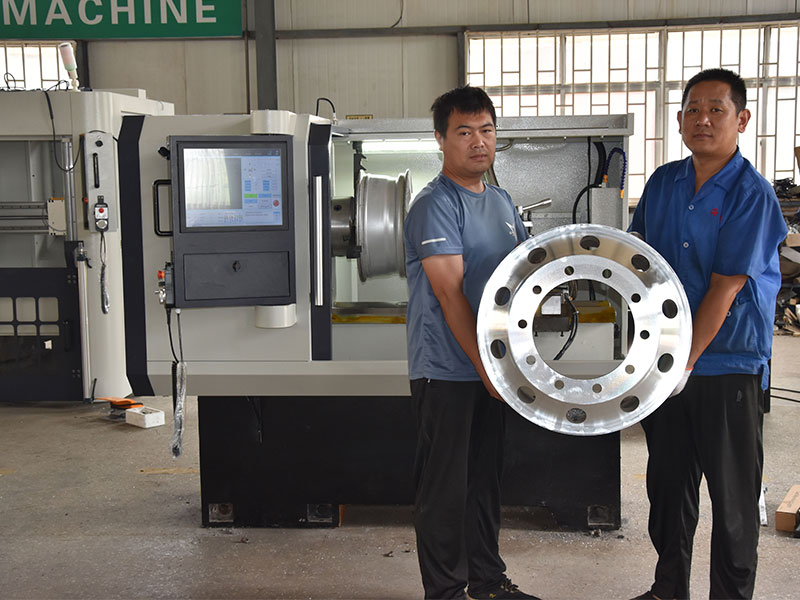
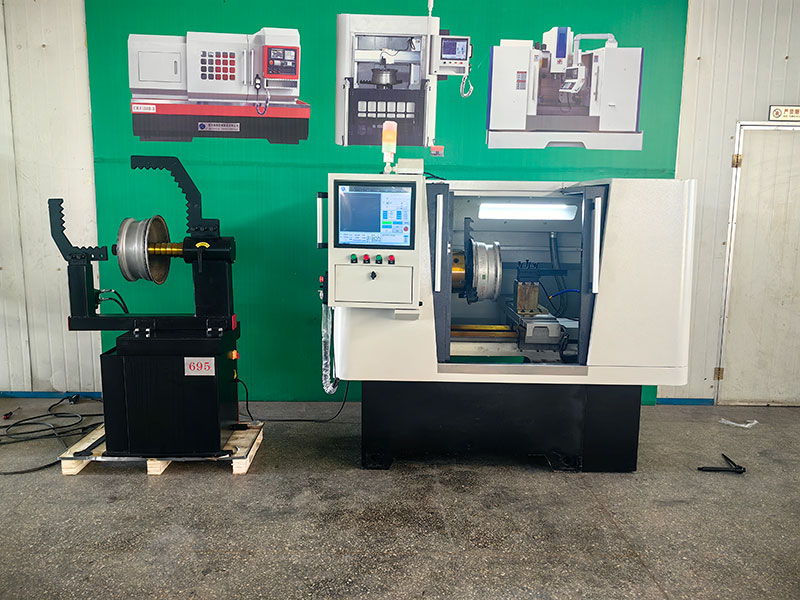
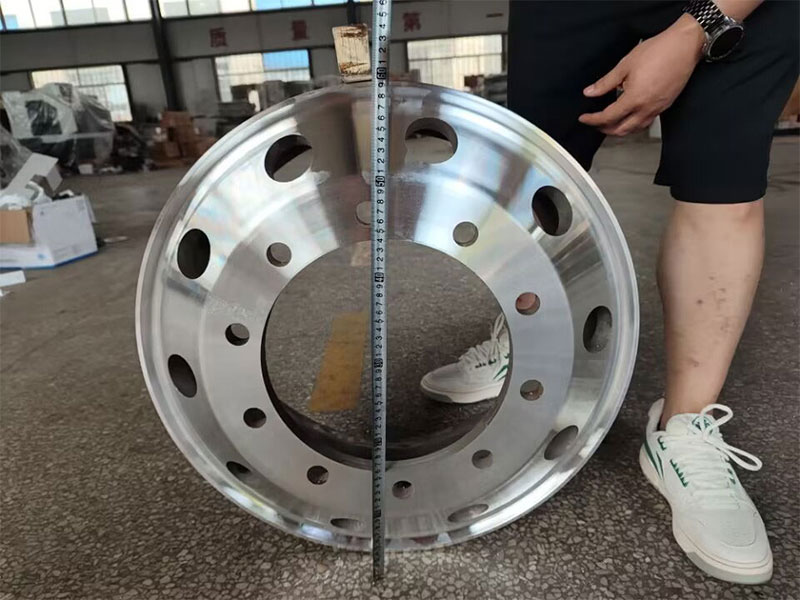
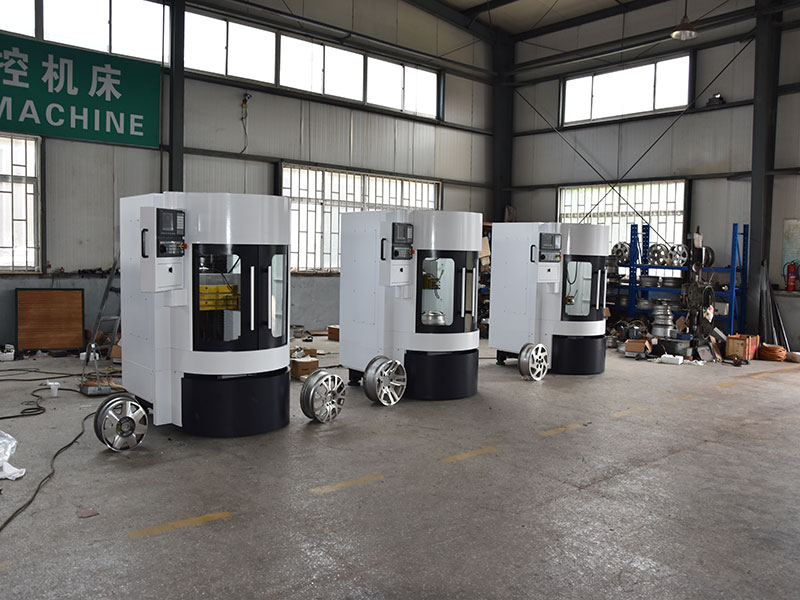
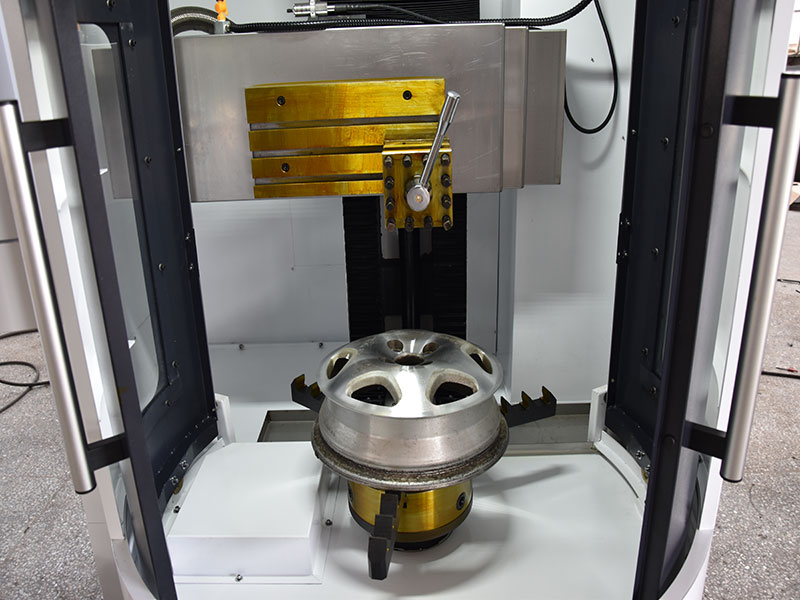
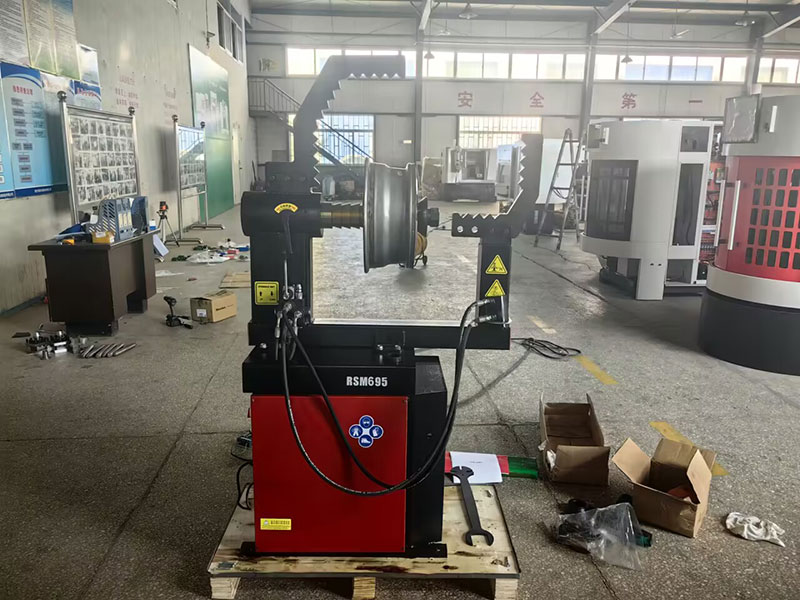
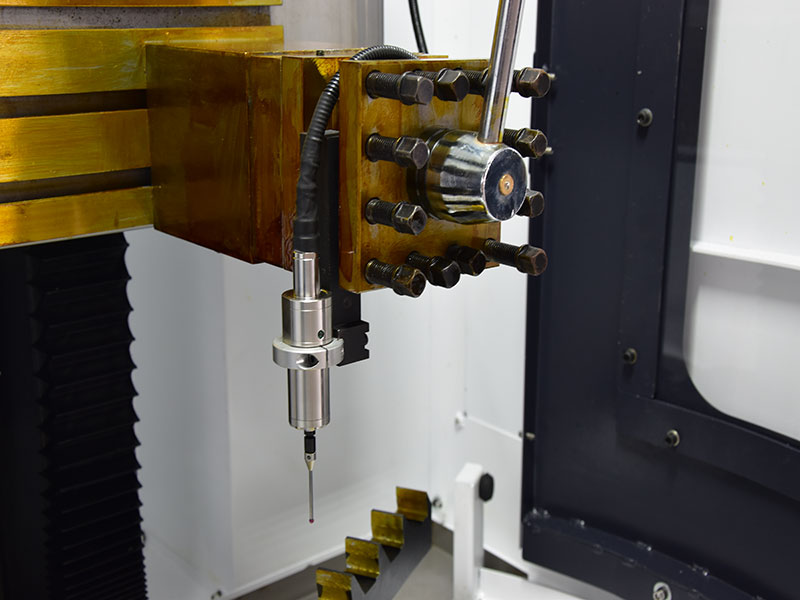
4. How Does Taian Haishu’s Alloy Repair Machine Enhance Efficiency?
4.1 Surface Brushing Treatment
Once the wheel has been reshaped, it can be paired with Taian Haishu’s wheel repair lathe for surface brushing treatment. This process is critical after reshaping or cutting, as it prepares the wheel for further finishing. Taian Haishu specializes in manufacturing automotive aluminum wheel CNC lathes, also known as wheel brushing machines.
4.2 Advanced Detection Systems
After mounting the wheel to a special extended claw chuck, the wheel surface data can be collected using Haishu’s laser detection system. This detection process takes only about 15 seconds. For clients requiring probe detection, our system supports this method, although it takes around 10 minutes due to point-by-point analysis. Additionally, Haishu has developed blade tip detection functionality, ensuring accurate assessments even for deep-rimmed wheels.
5. What Are the Benefits of Path Optimization in Alloy Repair Machines?
5.1 Traditional vs. Modern Optimization Methods
Traditional optimization methods often fall short of meeting the fast-paced demands of today’s market. Manual memory of coordinates or exporting paths for special input into wheel optimization software is time-consuming and labor-intensive.
5.2 Automatic and Manual Optimization Options
Taian Haishu’s alloy repair machine automatically enters the optimization path after detection. We offer both manual and automatic optimization to our customers. Automatic optimization is ideal for wheels with relatively smooth surfaces, while manual optimization is recommended for those with significant curve changes. This flexibility is user-friendly, even for operators without prior optimization experience.
6. How Does One-Click Programming Simplify Operations?
6.1 Simplifying CNC Programming
Based on the optimization process, we have developed a one-click CNC program output feature. Traditional programming can be complex and demands high skill levels from workers, which significantly increases labor costs. Taian Haishu’s one-click program output effectively reduces programming difficulty and saves costs, allowing operators with no background to achieve results similar to senior technicians.
6.2 User-Friendly Tool Setting
For those concerned about complex tool setting operations, Taian Haishu provides a one-click tool setting function. This feature allows for easy X and Z-axis tool settings, enabling workers unfamiliar with CNC lathe operations to perform tasks effortlessly. This greatly reduces time spent on complex setups.
7. How Is Processing Managed with an Alloy Repair Machine?
7.1 Efficient Processing Start
Processing is initiated with a simple one-click start, enhancing efficiency. If any path deviations are detected during processing, coordinates can be modified in real time. This capability allows for immediate adjustments, ensuring that the processing path remains effective and precise.
7.2 Additional Procedures After Processing
After completing the surface brushing treatment of the wheel, further procedures may be required, depending on customer needs. These can include wheel painting equipment, wheel ovens, wheel cleaning equipment, wheel electroplating, tire changers, and wheel balancers. Each step is essential for delivering a finished product that meets customer expectations.
8. Conclusion
In this overview of Taian Haishu’s alloy repair machine, we have highlighted key features and processes involved in alloy wheel restoration. From initial reshaping to advanced detection systems, path optimization, and efficient processing, each aspect is designed to enhance the performance of the wheel repair machine.
If you have wheel repair business needs or wish to learn more about Taian Haishu’s wheel repair equipment, we invite you to contact us. You can reach us via phone, email, or by visiting our factory directly. We offer customized services and are available 24/7 to support your wheel repair business.
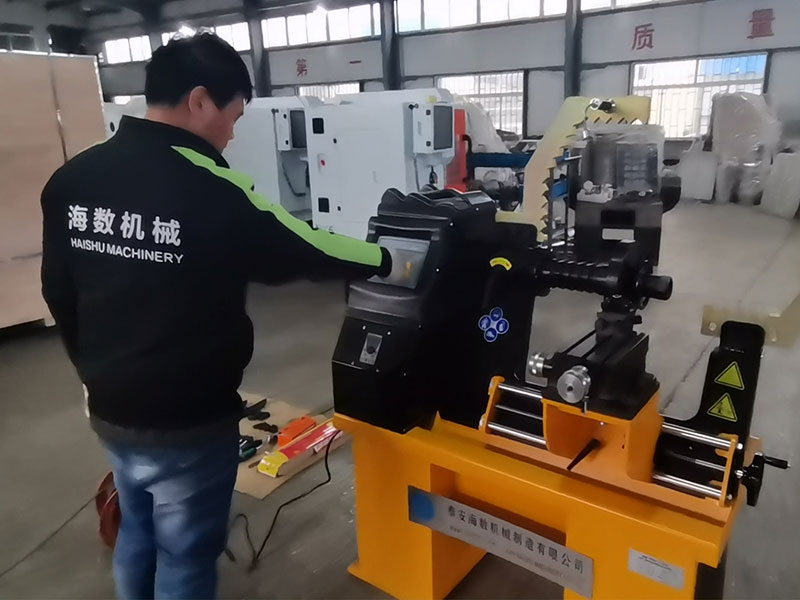
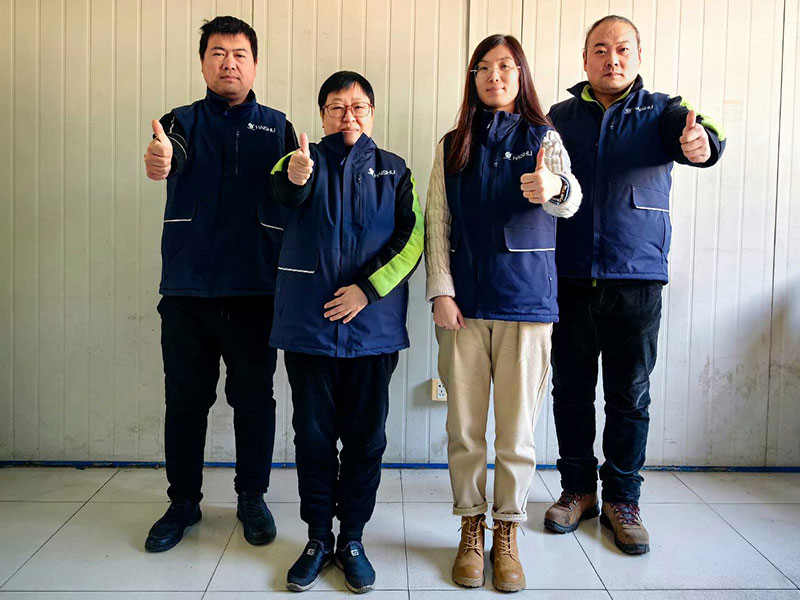